
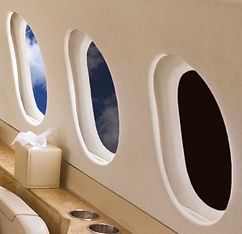
Freshbook Feature



Honestly, the possibilities are unlimited. We really don't like to say no, ever. It excites me when a customer comes with something that's very different - very challenging that affords us an opportunity to learn and grow and be able to offer new things. So we're we're constantly experimenting.
- Nichole Kalogridis
Continued from main page . . .
RR: Allright so that brings up a question that I didn't have scripted. So, I think what I'm starting to understand is that you start with Nomex and then you then you lay whatever the customer specified material is over that - you bond that to it and then apply a pressure treated die to achieve the design…or how does that work?
NK: Not necessarily. So, when we first started with Deconel, we knew we needed to use a Nomex fabric because its what was needed to pass the commercial aerospace testing. Nothing else on the market was able to pass the OU 65/65, which is not a fun test to pass.
RR: So that was only needed for heat release, smoke density, and toxicity?
NK: Yes, only for commercial aerospace but tough to pass. So that drove the need for our Nomex fabric and we've traditionally used Ultraleathers and Ultrasuedes in a business jet environment however, with a lot of work and I'll thank Emirates for this, we had a designer out of France come to us with their proposed design for Emirates and that fabric was a commercial grade material, but had never passed with a foam buildup for this type of application and associated testing. It was a Tapas product, made by Tapas and we were tasked with getting it to pass so I spent seven months working with different buildups and ultimately succeded. We were the first company to get Ultrasuede or Tapasuede and foams to conform and pass the 65/65 for commercial bulkheads.
RR: Impressive and a testament to perseverance. But I want to come back to the relief design itself. Is that a pressure thing, like with a die?
NK: It really depends. Most of our work is done by hand. There are some that we machine out if it's a heavy 3D effect. And some of it is of course is a patented process but again, a lot of it is handwork because of the need for precision. If we need to use machinery to get a shape just right, we'll make sure the design matches the drawing but it is very hand heavy just because it's easier to control that way and especially because we're providing single sheets of material - often for a 20 foot long window panel. That's not something you can get really have thermoformed from a practical perspective. I don’t even want to know the cost, not to mention the lead time. Just to have a plate made for a much smaller part we've paid $7000 for a thermoformable mold - so it's not really something that's very feasible for. Our work is very custom and I have customers that say we need a sample in three days there's no way that we're going to get a plate made and press that in anywhere near a time-frame like that. In addition, I have not found that thermoformable foams hold their memory as well as the hand techniques we employ. We welcome technology of course, but only when it makes sense.

Yes, we are busy now working on our new collection for NBAA. It will be a collection of entirely new designs, heavily focused on nature and patterns actually found in nature.
RR: In looking at your Selected Portfolio on the website, it looks as though you have incorporated fiber optic lights and some other pretty sophisticated designs for your clients. Can you talk a little bit about that and give our design subscribers an idea of the range of possibilities that are actually feasible?
NK: Well, honestly, the possibilities are unlimited. We really don't like to say no, ever. It excites me when a customer comes with something that's very different - very challenging that affords us an opportunity to learn and grow and be able to offer new things. So we're we're constantly kind of experimenting and a lot of R&D.
RR: I see. So, thus far at least, you really haven't encountered anything that is beyond your capabilities? It sounds like you’ve just said, hey let's go for it and we’ll figure it out.
NK: Yes, that’s pretty much our stance. It helps us grow and get better, so very little downside. I mean sometimes we may need help. Like maybe we need a strip of wood veneer to make the design work. We go to somebody that specializes in that and we bring it in and find a way to incorporate it into the buildup.
RR: I get it. Actually, sounds like a fun stimulating process. What about the fiber optics part? I think you were going to comment on that.
NK: Yes, so as far as fiber optics go, many of our customers are kind of afraid of using fiber optics and so we don't get a lot of call for it. I think they believe it's just not possible or it'll overcomplicate things, etc. Now for our carpet of course, it’s a different story. We can install the fiber optics into the carpet’s latex backing in a way that let’s us roll the carpet and ship it. With Deconel, it's a little different and since the fiber optics needs a substrate to apply to, we would need to work them into the panels themselves. But we can do the installs in house when called for.
RR: OK thank you.
NK: Yes, so, in follow-on, they wouldn't have to worry about it. They could just send us the panel, we would prepare everything and it would be ready to plug and play.
RR: Looking at some of the offerings on your website, it appears that in some cases there are multiple materials comprising the design. I know you’ve already touched on that a bit but can you elaborate? Is that a fairly common occurrence?
NK: Sure, so, let’s say we're doing a decorative bulkhead. We've got different techniques that allow us to puzzle piece that together. If we (or the designer) want to use four or five or six different materials - or even do embroidery across multiple fabrics or what have you, we can accomplish that, and yes it’s a fairly routine occurrence for us. We can also do an applique of a logo or something like that – also something we’ve done multiple times.
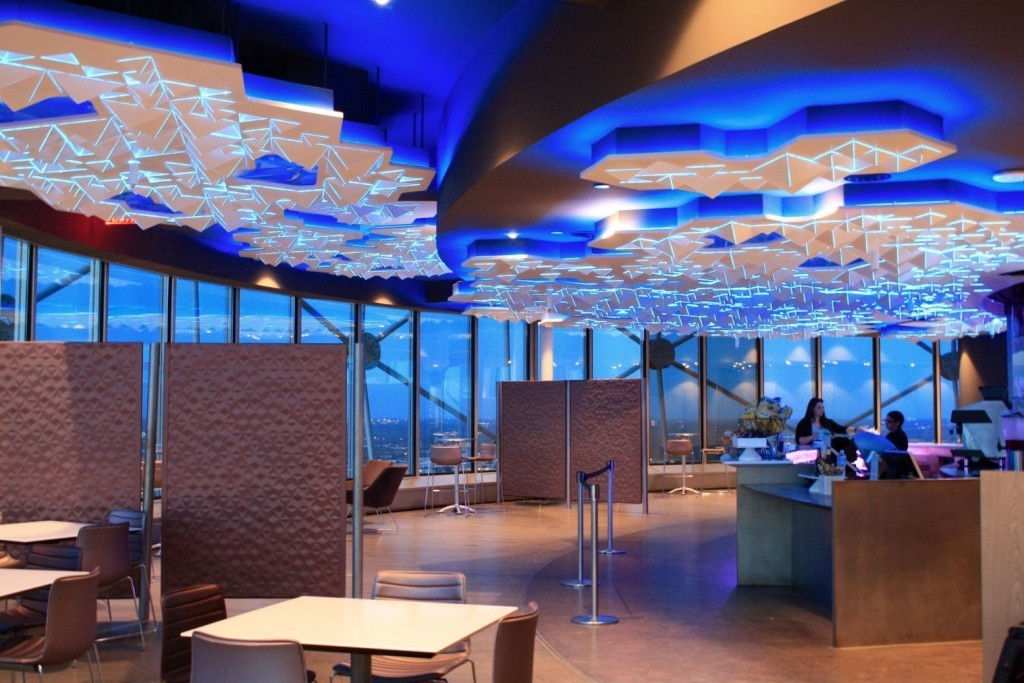
Installation: Cloud Nine Hotels & Resorts
RR: Ok well thank you for putting a finer point on that. So, you just mentioned bulkheads and on your site, it lists ceilings, wall panels, partitions and galley structures. That’s a pretty wide range of applications. But I’m wondering, have you ever had requirements for such elements as hard back chairs? I mean hard shell chair backs or perhaps even window shrouds or other less common areas?
NK: We have done a couple of samples for window shrouds though I think that's typically a fabric material in which case we would just be sending along the fabric vs. actually working on the window shroud itself. If they wanted us to embroidery the fabric or do some design work, we certainly can but that's about the extent of it for window shrouds.
RR: I see and what about natural leather?
NK: Yes, we incorporate natural leathers a lot. As an example, we are working with Green Hides and are their preferred stitcher. So, anytime they have a project with stitching (generally seat inserts) it comes to us. And what I've been trying to promote is our embroidery capabilities which are way beyond what most companies offer. It allows us to be very decorative, even on intricate designs or patterns. We want to offer a more decorative seat back - not just the typical diamond stitching that’s so common these days. And we could have multiple colors and layers and lots of texture. It’s simply because we’ve got more sophisticated machinery – as well as the desire to do it - because it's a lot of work to figure out. And then we have to figure out how to make everything pass burn. A big part of taking on these challenges, for me anyway, is that I'm an artist and I want to see cool stuff. But it is a lot of work the things that we do. We're using handwork machinery and a variety of other techniques – and so it can get pretty complicated melding all those together.
RR: Well, our readers will certainly love hearing that. Breaking new ground often boils down to who’s willing to take it on vs. sticking with more predictable requirements. My next question is, are any of your surfaces platable? That is to say, have you ever utilized 3d printed parts that can then be electroplated or powder coated? And if so, what range of options would the designer have in terms of the final finish and colorations?
NK: Well, we've done some gold leafing in that manner and I guess we have done some 3D printed metal parts that were then plated. But we don’t have a 3D metal printer in house because we just don't get enough call for it. But of course, we have contacts that we work well with and so yes, we can outsource that part, have it plated and then incorporate it into our completed deliverable. As an example, we recently completed a lattice design for a bulkhead and that was plated. The design was laser cut and then plated and then embeded into our Deconel piece. We've also done some customer logos in metal that were then inset.
​
RR: Can your materials be installed or manufactured to conform or otherwise install onto compound curves or contoured surfaces? Like perhaps a dome ceiling curving in multiple directions?
NK: Well, generally speaking yes. We do it often. But it can depend on the stretch of the surface material. We do have some restrictions there but generally we don’t run into requirements we can’t handle in that regard.
RR: OK cool. Lastly can you explain a bit about the philosophical relationship, if any, between your mainstay ‘carpet’ and Deconel surfaces? It would be interesting to learn how your product offering migrated in this direction and if perhaps it was customer driven or simply an idea that seemed compatible.
NK: Well again it sort of goes back to the story when my father needed a better, lighter weight solution for the bulkhead tapestries. So the connective beginnings were there and the connective tissue I suppose, is that we are simply always seeking new ways to meet our customers need for new aesthetic treatments that can be certified.
RR: When was the name Deconel formally rolled out?
NK: I will say 2006. I believe that’s right. And the division has steadily grown since that time.
RR: Finally, I’m sure our readers would like to know if you have anything new rolling out, wholly new products perhaps or new techniques?
NK: Yes, we are busy now working on our new collection for NBAA. They will be entirely new designs heavily focused on nature and patterns actually found in nature. Also, we are working on some old Japanese techniques and things like that. So yes, we are actively developing some new things and with new techniques. We’re also toying with some new embroidery techniques - a combination of multiple fabrics, multiple techniques, stitch patterns etc. Again, I am an artist and I get tired of all this diamond stitching and yes that's wonderful if the customer is happy with that but I would rather create something that is a functional art piece. It affords the designers a broader palette to create from.
RR: Yes, I can well imagine that designers enjoy working with you as an artist because in effect designers are artists. Almost all designers find it refreshing to be connected with somebody like that versus a technician or an engineer. In that sense you’re already speaking the same language. It’s always easier to convey a creative vision to another creative.
With that Nichole, I’ll say thank you for your time. It’s really been a pleasure and although many people are familiar with Deconel, I hope we’ve an opportunity here to expand that audience and educate them on the breadth of your offerings.
We look forward to seeing you the NBAA in Las Vegas later this year. In the meantime, for more information on Deconel, visit:
kalogridis.com/home/deconel/
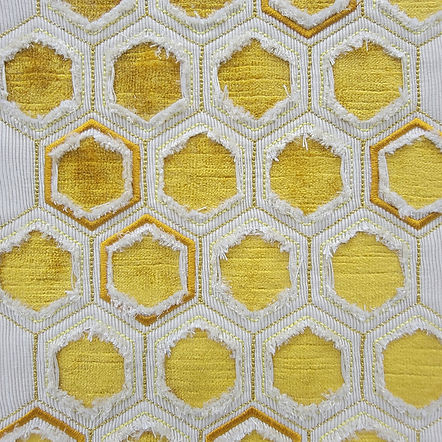
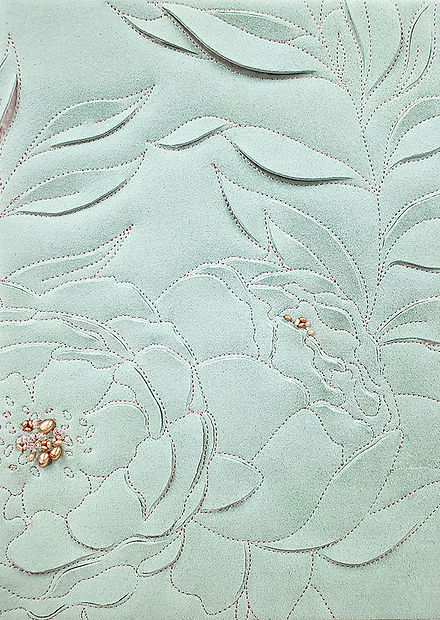

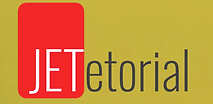