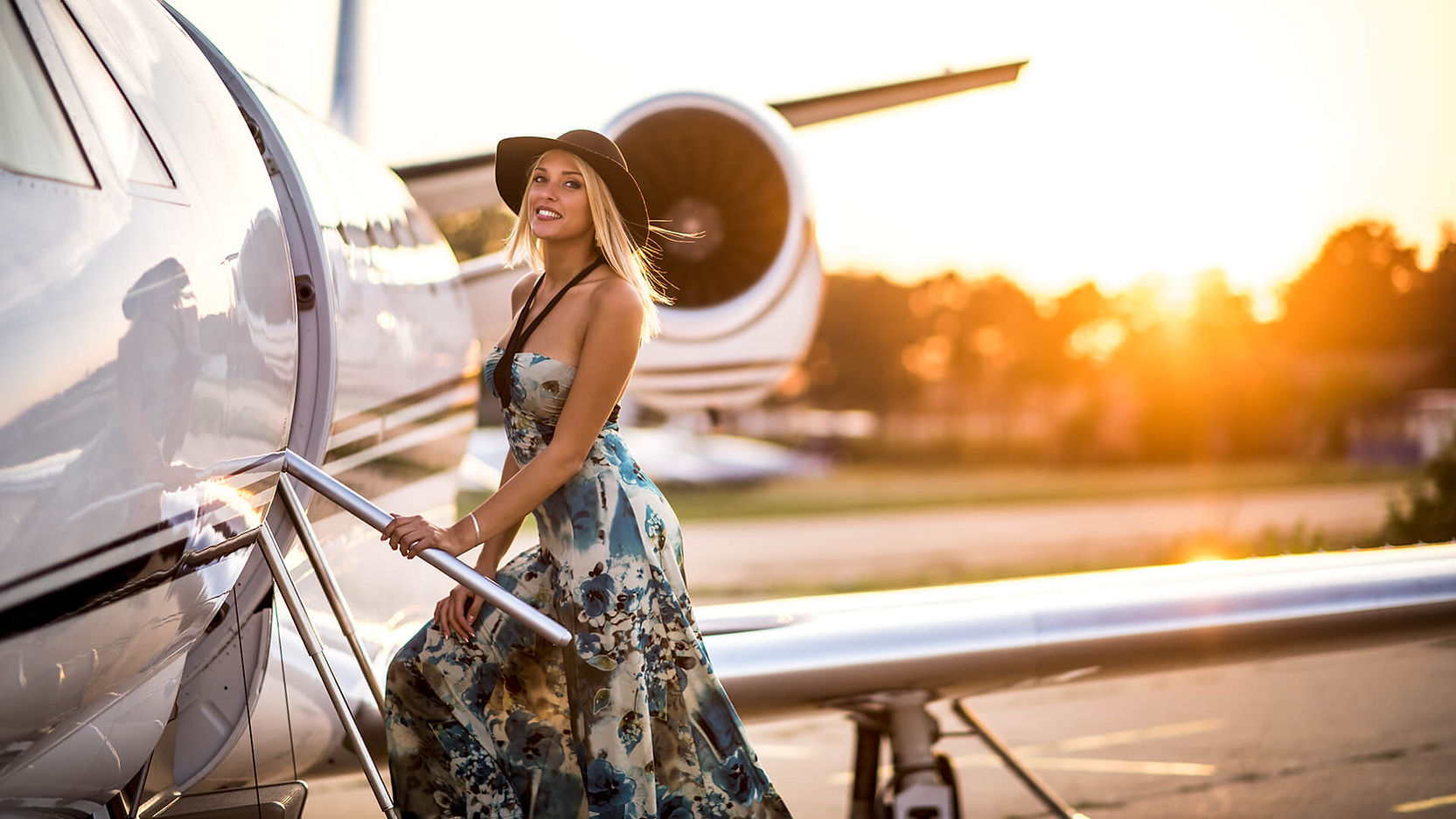

Issue 9 July, 2023

Issue 9 July 2023



F E A T U R E S
1 Winch Design - The UK's Super Studio
7 An American Legacy in Aviation Wood - Booth Veneers
11 Deconel - A 3-Dimensional Kaleidescope
18 Cabin Confidential - "Third Grammy Takes a Fall"
Issue 9 July, 2023
JetCabin Freshbook 2023 . all rights reserved
f r e s h b o o k . a e r o

Publisher
Editor
Editorial
Advertising
Directory Listings
RWR Designs GP LLC - Texas U.S.A.
Rick W. Roseman
directorylistings@freshbook.aero
Freshbook Magazine is a division of JetCabin Freshbook (freshbook.aero), and is an all digital publication, distributed globally to subscribers only. The subscription rate for any / all legitimate individuals or companies directly involved in the interiors sector of business or commercial aviation, is: $0 (no cost).
Advertising rates are available via our media pack.
Visit our Advertising page here.
JetCabin Freshbook
3206 La Paz Lane
Santa Fe, NM 87507 (u.s.a.)
If you change jobs or otherwise will no longer have a valid subscription email, please notify:
circulation@freshbook.aero
D E P A R T M E N T S
Boeing 787-9 at sunset / photo courtesy of Boeing

Words from the Editor
Well it's finally here. It's officially summer. I love summers because our social life moves outside . . . dinners, parties, veranda sitting and all the rest. But this year, in the US at least, we have something called a "Heat Dome". I literally have never even heard the term until it started showing up in my news feed. Here's one: "Heat Dome swelters the midwest" Here's another: "Texas Heat Dome inches north and east - advisories go up in 15 states!" But what the hell IS a heat dome? I don't see anything up there.
I think it's just the latest meteorological buzz term made up by some dicky wearing, g-scooter riding, pseudo scientist . . . probably in SoCal. And while we're at it, Meteorologist - seriously! Even at the spry age of five, I was aware enough to understand the stupidity of that one!, Clearly a mistake by one of Noah Webster's typesetters that aged too far to undo it. Even Google appears to be embarrassed over it. Three are four searches down, they finally offer up the botched attempt at a replacement handle for those that REALLY study meteors. Are you ready? Wait for it . . . METEORITICIST. Try to pronounce that! Imagine the latent anger and betrayal these people feel when they watch ABC's nightly news anchor introduce their slicked up weather-tool. "Now here's Meteorologist Rob Marciano." No offense ROB, but you ain't no meteorologist!
The handle was stolen and the entire planet-full of ROB's needs to give it back! Weatherman, Weatherperson (enter your pronoun) works just fine. I have no time for such nonsense and I summarily reject the whole Heat Dome scam. I grew up in Texas a hundred or so years ago and we managed to suffer through the intellectual vacuum of invisible domes to explain what we already knew. As my mom said, "It's Hooter'n Hades outside boys . . . drink some water".
​
But rants aside, I still love my summers. Show me a swimming pool with a bar next to it - and I'm happy as a clam!
​
Cheers!
​
Richard Roseman - Co-founder / Editor

First Visit? JCF Magazine is about jet interiors, and only jet interiors; the designers that design them, the centers that build them and above all, the cabin supplier groups - worldwide, that ultimately make it all possible.
If your company belongs to one of these groups, let yourself subscribe to something worthwhile for a change. Stay fresh, participate and grow .

VISION
We’re Changing the Way you think about Aviation Magazines
No flip viewers...no thumbing pages, no zooming to read text or adjusting scale to see images. Just smooth scrollable content, smartly written feature articles, full-width ads from the top companies in the world. Plus exciting departments that bring the FRESHEST in new rollouts and present the latest trends. Plus you'll always find glimpses of the near-term future of cabin design and products. And best of all, it's all interactive with video, live links and instant access to the people and extended content you're interested in.
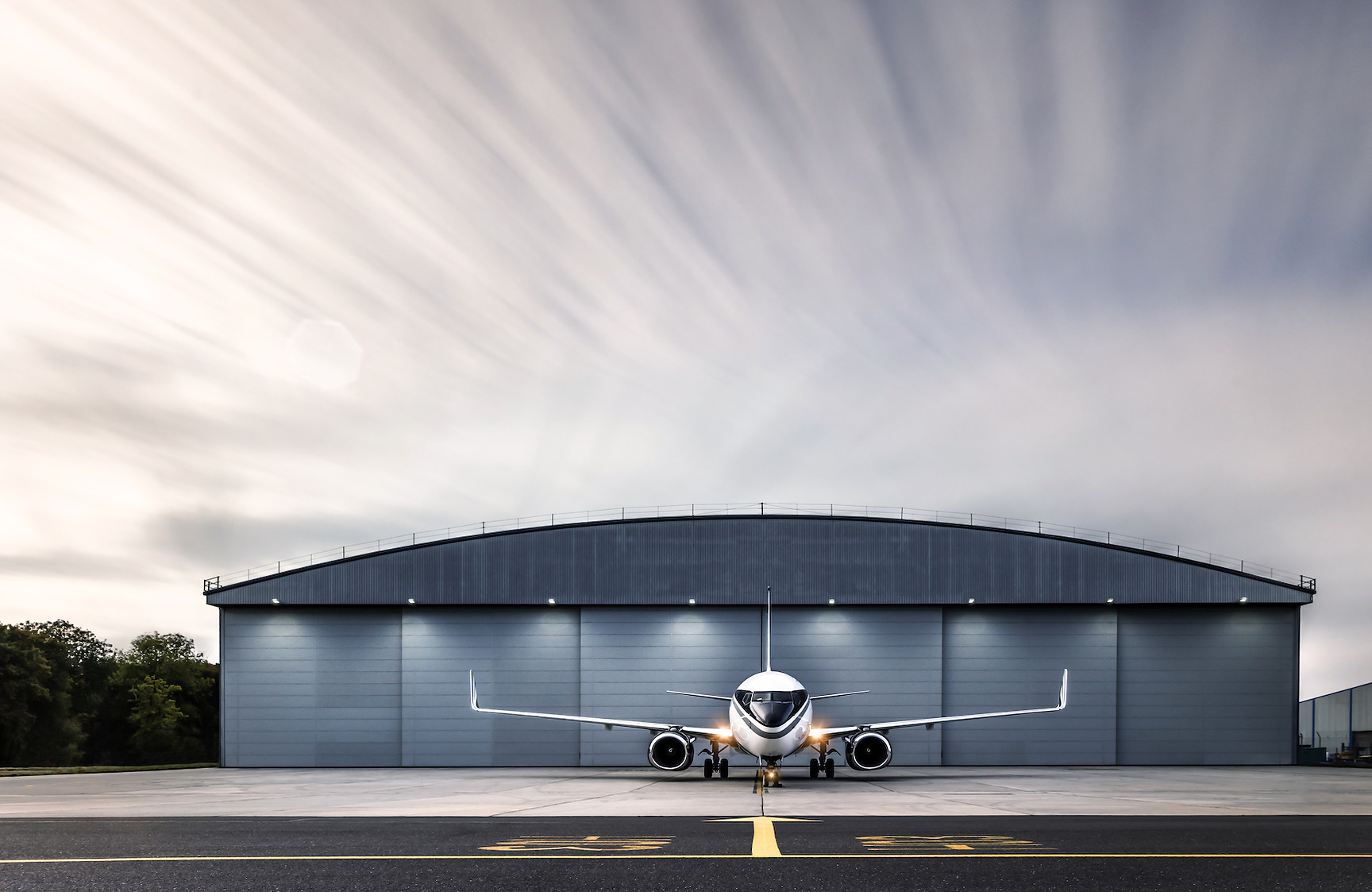
%20copy%207.png)
The UK's Super Studio
© 2023 Alexander Craker

.png)

By: Rick Roseman
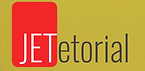
Scattered along the banks of the Thames in London are four infamous (and my personal favorite) landmarks. First of course, there is the Tower of London, right? None other than His Majesty’s Royal Palace and cannon protected stone fortress. Secondly is the iconic Palace of Westminster where Commons and Lords have bickered successfully for centuries. Third of course is the somewhat less historical Eye of London, which as I just discovered is not an ‘eye’ at all, but some kind of ginormous carnival ride hung out over the river with some cables. But for my money, it is the fourth landmark that I hold in highest regard; the Old Fire Station at Mortlake High Street in Southeast London. As with all good fire stations back in the day, it was (and is) poised on the banks of the serpentine Thames providing an inexhaustible supply of river water from which to arm an armada of horse-driven firetrucks endlessly tending to blazes around the city. But predictably, with all exceedingly cool, decommissioned old fire houses, they assume new lives either as highfalutin galleries, Bugatti showrooms or prestigious design houses. In this case, it was the latter when in 1998, design legend Andrew Winch and his wife Jane set their sights on the landmark and wrote the check. On that day in October, the Mortlake Fire Station became the new home and central headquarters for Winch Design, arguably the most renown yacht design studio in the world today. And with now some two dozen aircraft projects under their belt – certainly one of the most experienced and tenured studios in the aviation space as well.
Today, I was lucky enough to sit down with my pal Greig Jolly, a Winch partner presiding over Winch’s yacht & aviation divisions. As you will see below, we covered a lot of ground in our Q&A style interview – most of it focused properly on aviation and gathering the inside dope on why this firm has been so remarkably successful and why their tenured experience keeps their customers returning.
​
"Howdy Greig."
​
"Howdy Rick.."
​
“It’s a Friday evening - getting dangerously close to your cocktail hour there, so let’s jump in, shall we?
“Let’s do!”
RR: how long has your aviation division formally been around?
GJ: Let’s see, our first aviation project was back in about 2002 so a little while now - almost 21 years now. As for how that came around, we actually were approached by a client who wanted to build a sailboat with us because that was our core business at the time. That conversation led to our learning that he had just placed an order for a for a new BBJ. He liked what we'd been doing with his sailboat project and asked if we had any experience in aircraft. Obviously, we had to say “well, no but you know there's lot of close kinship between the two disciplines and the challenges of doing things right in small spaces etc.” We pointed out the parallels and challenges of multi-function spaces, lightweight materials etc. At the end of the day, it played out as this kind of weird, serendipitous situation where we said yes, fine we can do that for you. We'll have a go and yeah that was almost 21 years ago now. In fact, I was having a look the other day and we're actually about to deliver our 25th aircraft project. So, you know saying yes to that conversation and that client, it ultimately created a whole new arm of the business for the company.

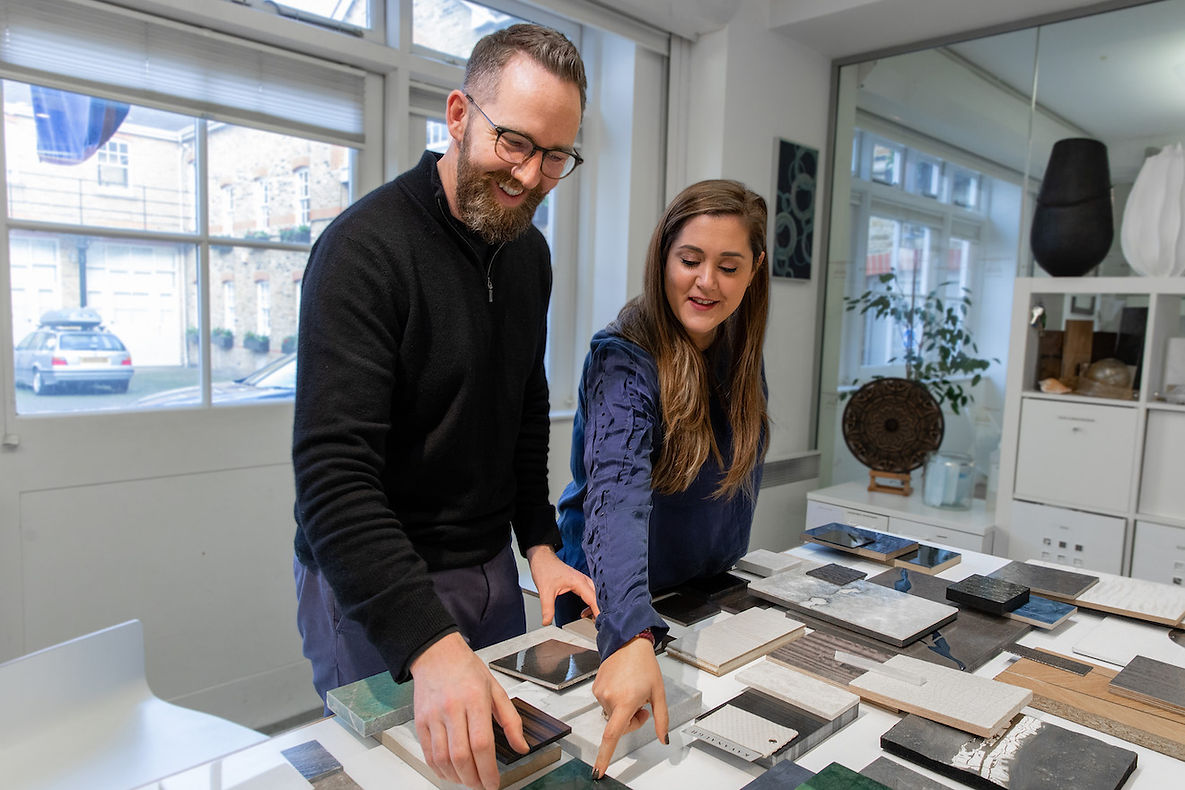
Old Firehouse at Mortlake High Street - WInch Design Main. Studio
Greig Jolly w/ colleague Mandy / Material Room
RR: As you mentioned above there's obviously a close kinship between yachts and aircraft but there are significant differences as well. In terms of your approach to VIP aircraft projects compared to a large yachts, what would you say are the biggest differentiators and what disciplines do you apply to in managing those differences.
GJ: Good question. I mean, as I was just touching on a minute ago, there's so much that we can share between the two disciplines there's so much to think about in both modes of transport. It's the same clients obviously. People who purchase large yachts generally have their own aircraft as well. So there's so much knowledge we can share and skills we can deploy between those two disciplines. In designing an aircraft cabin, there's so many constraints - so much more than there are on yachts. So, OK they're both methods of transport but you know the aircraft is what we call a true dynamic environment. It’s a moving object every time passengers are aboard, right? Versus a yacht which much of the time, if not most of the time, is anchored out at sea. When you're flying through the air everything has to be securely fixed to the fuselage. You have to have an extensive knowledge of the certifications that govern all that. Then there is the bonus of exhaustive testing for airworthiness. You've got cabin pressure and decompression requirements, blow out panels - all these kind of things plus dimensional restrictions. You know you don't often have a comfortable head height on an aircraft, especially if you're in a in a narrow body aircraft or a regional jet. So all of that is very challenging and which we have a significantly less of on the yacht side. We're a lot a lot freer there but in an aircraft, the floor plans, no matter how big or small, you're dealing with the constant section of tube. So, your layout is dictated by that and so the spaces become linear in terms of layout. Bedroom, lounge, dining etc, generally stacked one behind the other. Even when you’re given wide body you've got a little bit more room to maneuver, but it's still generally a very linear floor plan. And so managing the differences between the two is really just about experience and a keen understanding of the regulations and constraints of both – and then using these skillsets to make the best of each.
RR: So, mobility design is obviously a blanket term and a popular one these days but certainly if anyone can legitimately claim the territory, it's Winch. You seemingly have mastered both large seagoing yachts and wide body jets. Are there currently any other forms of transportation involvements for the studio and if so, was it an organic opportunity or something the firm sought out as a further diversification.
GJ: Again, good question but I think as designers if you're a good one, you should be able to turn your hand to anything really - whether it’s a watch or 100-meter super yacht – because as you know, the disciplines are the same; proportion and form and taste and color and everything else. With all the things we've done over the years and with such a wide portfolio it always invites new possibilities and genres of projects. We're known for doing sailing yachts and superyachts of course but we're also doing projects at the moment such as small day boats and carbon fiber racing boat hulls. We've done a few private helicopter projects and small refits of regional jets all the way up to wide body aircraft. We also did a concept for a train a few years ago; rail is marking a new area of mobility for us. We start the same with all clients, again from that yacht design point of view, asking about lifestyle, requirements, and objectives. And it inevitably takes us in new directions. As a unique example, we did a concept for an airship a few years ago, an amazing LTA project called HALO, that while not yet to fruition, may one day mark a whole new area for VVIP leisure flight.
A Lake, The Swiss Alps, The Jet Biz . . . What Are You Waiting On?
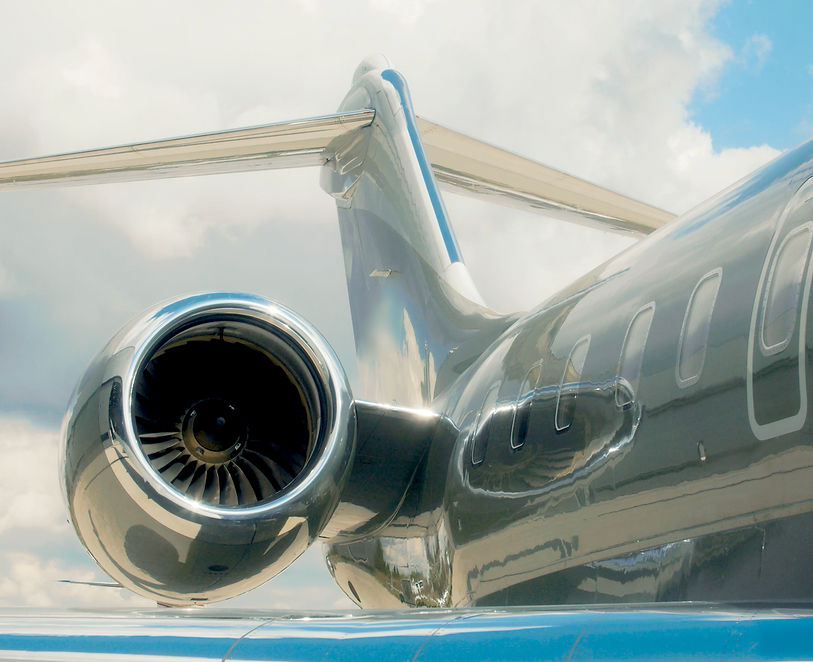

RR: In my experience PDR and CDR are certainly the two most critical and potentially pivotal moments in the in the life of a VIP aircraft project. Can you take us through the process a bit and tell us about what you've learned about navigating these two junctures for maximum success?
GJ: Wow, this could be a long answer Rick (he chuckles) I read this one when you sent the notes over and I was like wow we get it we're getting in deep now!
RR: Yep, I hear you, so let's do this. Let’s forego taking us through the process because that indeed will be a long ride and if we're gonna get you down to the pub before sundown for heaven’s sake, we better ratchet it back. Instead, perhaps you could tell us a little bit about how you approach PDR and CDR – some of the practices you employ in getting through them productively etc.
​
GJ: OK (grinning, wiping his brow) So, for us they're exciting kind of milestones and as you suggest, they’re big and culminating milestones for the design portion of any large aircraft project. It's where you're moving from your sketches, your vision, your renderings etc. into really integrating all that matter with the engineering from the completion center and the certification body. It’s serious and it commands the attention of everyone involved. It’s normally a point in the project, especially CDR, where there's some big decisions to be made and as you well know Rick, once you get past that CDR point, there's no going back because there are thousands of hours of engineering behind every cabinet on that aircraft. There’s stress test, burn testing a whole host of regulatory concerns - and again all the engineering. If you get it wrong heading into CDR, if your drawings are wrong or you’ve made incorrect assumptions and something doesn't work in a real-world sense, it can wind up being a very costly mistake. It really forces you to focus on the detail of what you're doing. So, in that sense it's kind of a scary point in the project where everything starts getting real. But it's also that point in the project where collaboration becomes really important. Collaboration with the completion center, with the FAA or EASA, with the engineering body and on and on. And sometimes you have to pick your battles. You have to know that not everything in your design is gonna make it through engineering and you have to be willing to make those judgements and those sacrifices in the best interest of the project and your customer. There often are weight reasons, cost reasons or schedule reasons that make a particular design component not feasible. And they’re often things you can’t know until you arrive at PDR, but they’re valid. It's where you've got to decide which bits of that floorplan or your architecture are going to really hold and whether the end justifies the means in terms of a battle with engineering. The old you know, designer versus engineer kind of head butting is normal to an extent and to be expected. But you can’t have it impede your project and so a spirit of healthy collaboration has to prevail. That’s the way you get there.


BBJ Max Concept by: Cheryl Pelly Design

"The top DESIGN studios around the world are absolutely the ones that inform the industry and set the new trends."
Jetzign is where we highlight the very latest from the top designers and studios. Whether it be the iconic independents or the great design departments within the world's top completion centers, this is where you will find their latest works - and always with an emphasis on the near-term future of cabin design.
SkyYacht ONE / courtesy: Sotto Studios
Richard Robledo 1973 - 2023
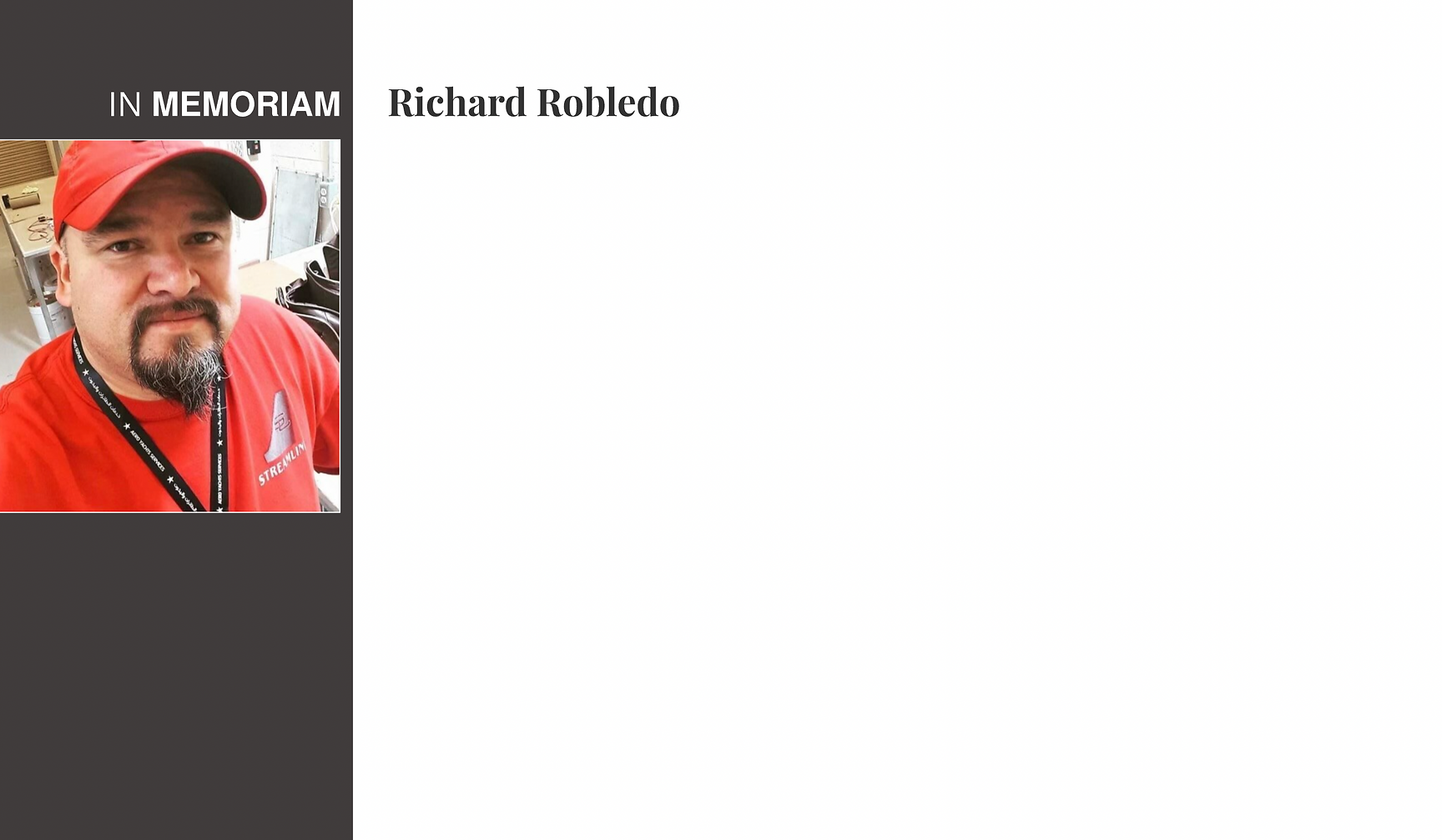
Every time someone in our lives passes, we stand up and say nice things about them. But let's be honest, in a fair amount of cases, we're recalling the best parts of who they were and sort of leaving the rest alone, out of respect for the family. In contrast to that, Richard Robledo, is one of those guys for whom no one ever cast an ill statement. He was, in the very truest sense, "A Prince Among Men" - a man whose reputation most often entered the room before he did, a man for whom humility was intrinsic, rather than learned . . . and last but not least, a father and a husband of the sort that most only see on Hallmark. As he told me in a call just after Christmas this year "my girls are the center of my universe" . The girls to which he referred: His wife of 19 years Brigida and daughters Athena (18) and Aubree (12).
Yet for most reading this, we knew Richard professionally. And for those that did, we were in awe of his talent. I too knew Richard professionally long before I got to know him personally. I met him at a time when VVIP was still relatively young - and a place (San Antonio, TX) that was the mecca of US based VVIP aviation interior talent back in the early 90s. As alluded above, his reputation preceded him and that's how I first learned of him as well. Word of his highly specialized talents had spread like dandelions across the industry. I, like many, needed his rare brand of talent to make the impossible, possible and create magic for my client. Even though Richard left us at far too young of an age, he was already something of a legend even in his early thirties. He could do things that mortal men simply couldn't. He was a faux artist extraordinaire . . . a kind of 'magician' for many of us. And if he liked you and took your job, he was damn sure going to make you look good - which he certainly did for me on numerous occasions. Richard Robledo was one of those guys you loved to brag about over drinks or swapping stories at a show. Amid a world of otherwise fairly predictable products, services and innovations, Richard was the one vendor that not only produced magic tricks - but did it entirely by hand, a rarity in our industry - and our time.
It was him, some paint brushes, paints, resins, some clear-coats, and secret compounds, and an array of improvised tools that were his stock-in-trade. Oh, and he wasn't worried about you peering into his little treasure trove of implements - because even if you understood their use and watched him for hours . . . good luck trying to recreate what he produced. Only Richard knew that - and it only kept his magic more in the mystical realm. The stories of Richard's enigmatic talents are rich and abundant across VVIP interior circles -worldwide. I was privileged to have levied Richard's rare talents onto some of my projects. And each time, he indeed made me look good to my clients. But I am far prouder to have called him one of my best friends.
You will be missed by us all!

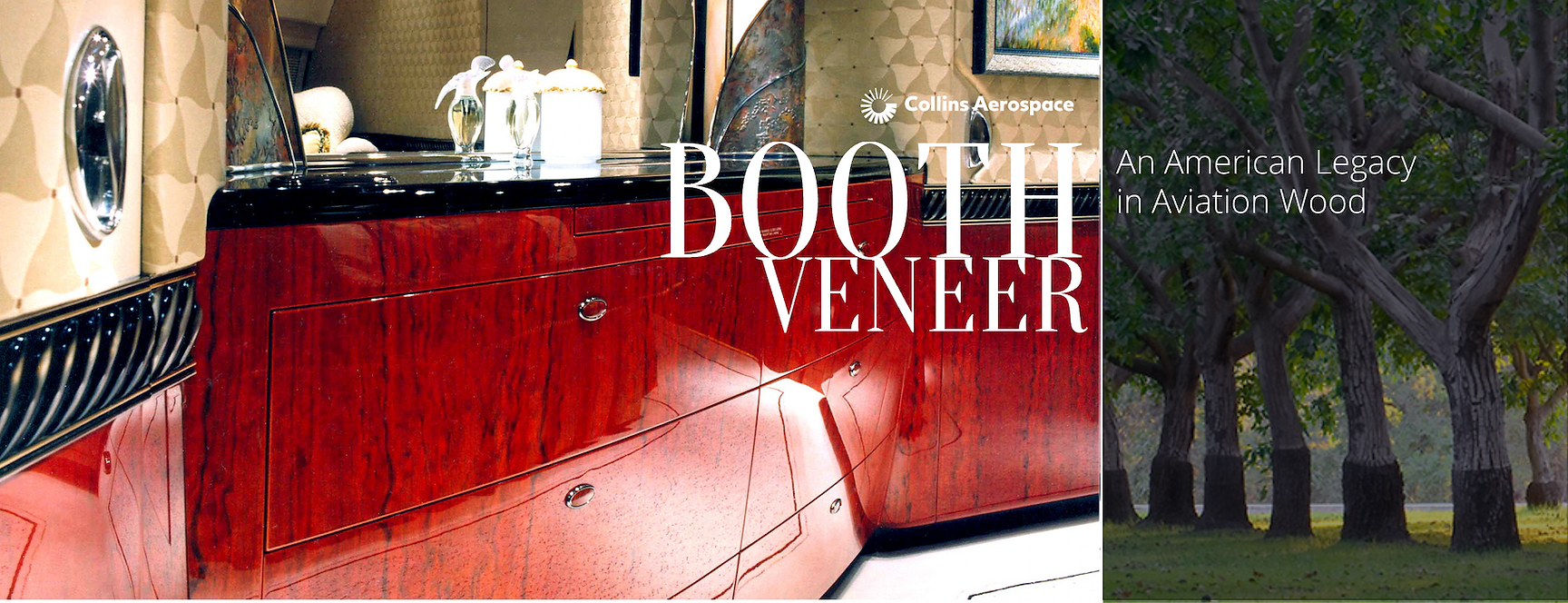
%20copy%206.png)
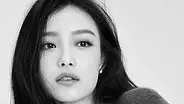
by: Melissa Tokoriyama - Special Contributor

You probably won’t find a lot of travel sites touting the exotic virtues of southeast Indiana. Oh, it’s beautiful enough mind you, but there’s no theme parks, beaches or metropolitan cities, just some inviting pastoral countryside nestled up next to the Ohio river. One of the picturesque burgs along the Ohio’s banks, is Jeffersonville, Indiana, county seat of Clark County and an undisputed mecca of furniture grade timber. Often called simply Jeff, its abbreviated handle, the town of 44,000 sits across the river from Kentucky just north of Louisville. But more importantly, Jeffersonville is home to one of private aviation’s legendary names, Booth Veneers. And as I found out, it’s quite an interesting story how this rather unassuming little corner of US geography – and this famous little company - came to be what it is today. Firstly, Jeffersonville sits right next to New Albany, Indiana an only slightly larger township but with the reputation of being the veneer capitol of the world.
And it didn’t happen by accident. Way back to the early 1800s, masterful woodworking craftsman from all over the world flocked to the area in order to bring their talents to bear on what at the time was a booming business; Steamboats – both the ground-up building of them and their stately interiors. The dense forested surroundings, the railroad, and of course the Ohio, all came together in a perfect storm for the manufacture of plywood and pretty much every other form of wood consumables.


But what really ignited the fuse was a big city investment firm out of Chicago. Near the close of the century, they had ‘seen the gold’ and began pouring money into the area until by 1920, there was more plywood and veneer manufactured in the little town of New Albany than anywhere in the world. So, by the time the now legendary Mr. Carl Booth was coming up in the late 1950s, the stage for what would become, was firmly set. But Booth himself wasn’t always a veneer purveyor. His early professional life was that of a schoolteacher. But eventually his love of wood and his own very accomplished craftsmanship won out, eventually founding The Carl Booth Company, now simply known as Booth Veneers, a subsidiary of Collins Aerospace.
As a designer myself back in the day, I was one of Booth’s customers on several projects and to this day, I’ll never forget that wonderful pungent smell of freshly hewed timber on entering their facility the first time. But even more than that, I can’t forget what an education I received in the selection and process of aviation veneers. I was a baby at the time, still in my early thirties and apart from having a raw vision or color and grain character in my head, I knew literally nothing. On that same first visit, the team at Booth took me through the process over the course of a long day – and by the time I left, they had not only found my perfect log, but I walked away with a knowledge of veneers that would serve me for years to come on other projects.
​
Continued below. . .
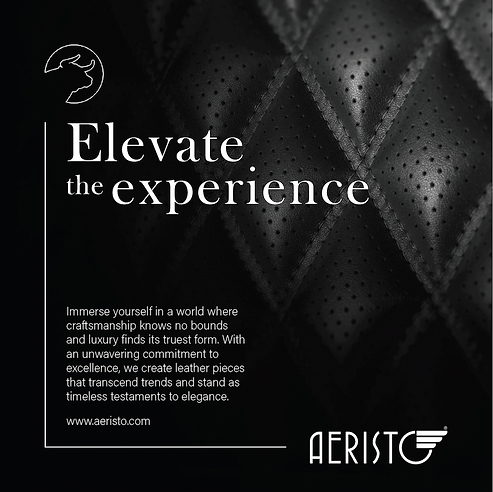
.png)

Today, I had the pleasure of sitting down with three of Booth’s department heads for a frank discussion and Q&A about the truly fascinating aspects that go into the process and production of the amazing wood veneers that wind up on the most expensive and beautiful VIP jets in the world. Here’s our conversation:
JCFM: We all know Booth Veneers. A legendary company. When did Carl first found the business and was he always focused on aviation or a combination of spaces?
BV: Carl was a high school teacher and had been an avid woodworker for many years. He was quite accomplished, and his work was recognized by someone at Ovation guitars who asked him if he would make faces for their guitars. Carl provided these faces using exotic, high-end wood for a while working out of his garage. One day he got a call from someone who had an Ovation guitar and loved the wood on it so much they asked if Carl could put that same wood on their helicopter. In typical Carl fashion, he said yes, having no idea how he would get the wood to pass the aviation flammability requirements. Through a lot of research and experimentation, he found a chemical solution to treat the wood to make it pass FAA requirements. He truly was the pioneer of aviation veneer and founded the business in 1976. Through the years, we have done some yachts and architectural programs, but the focus has always been on aviation. Everything we do is custom, and it really is our core competency.
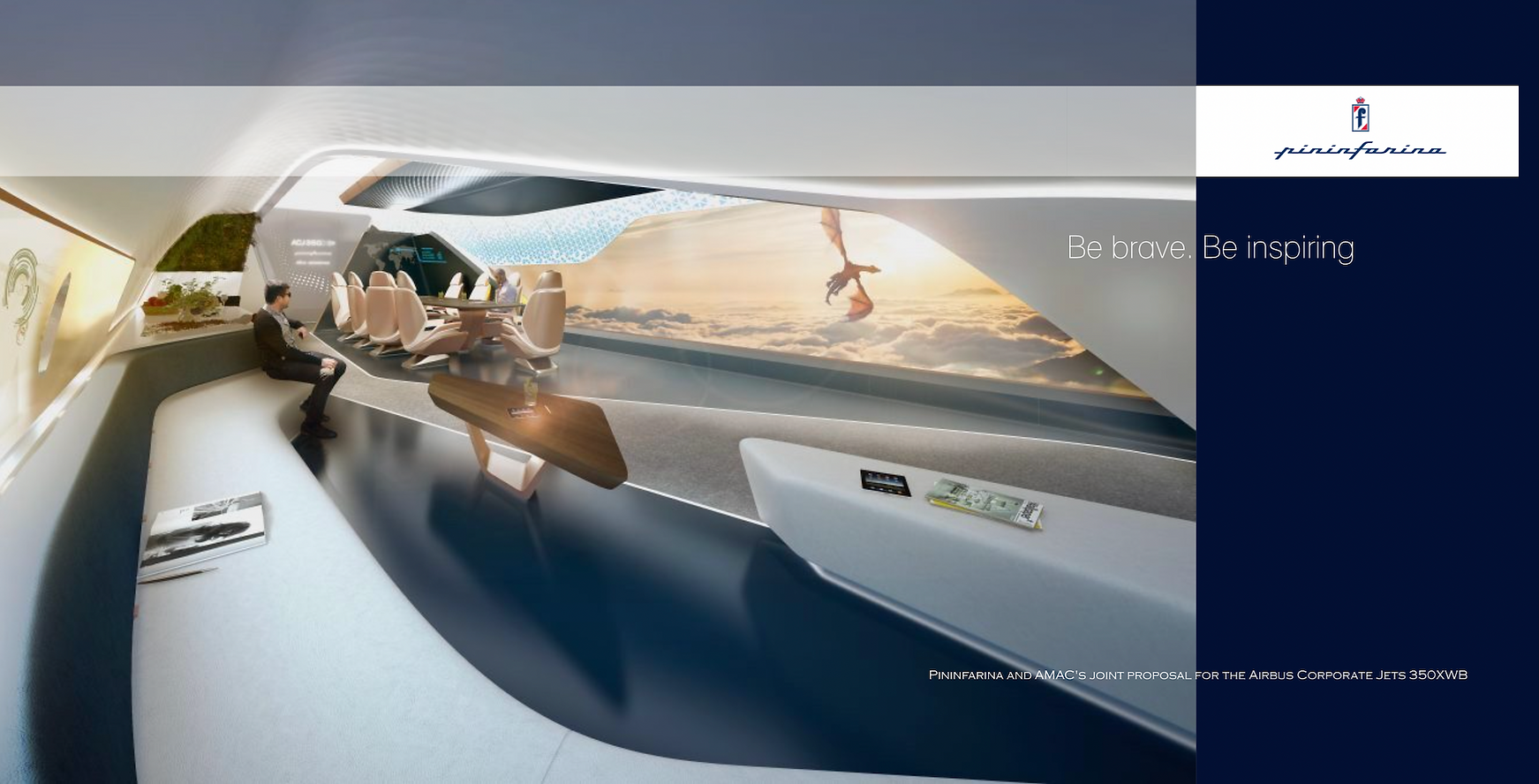
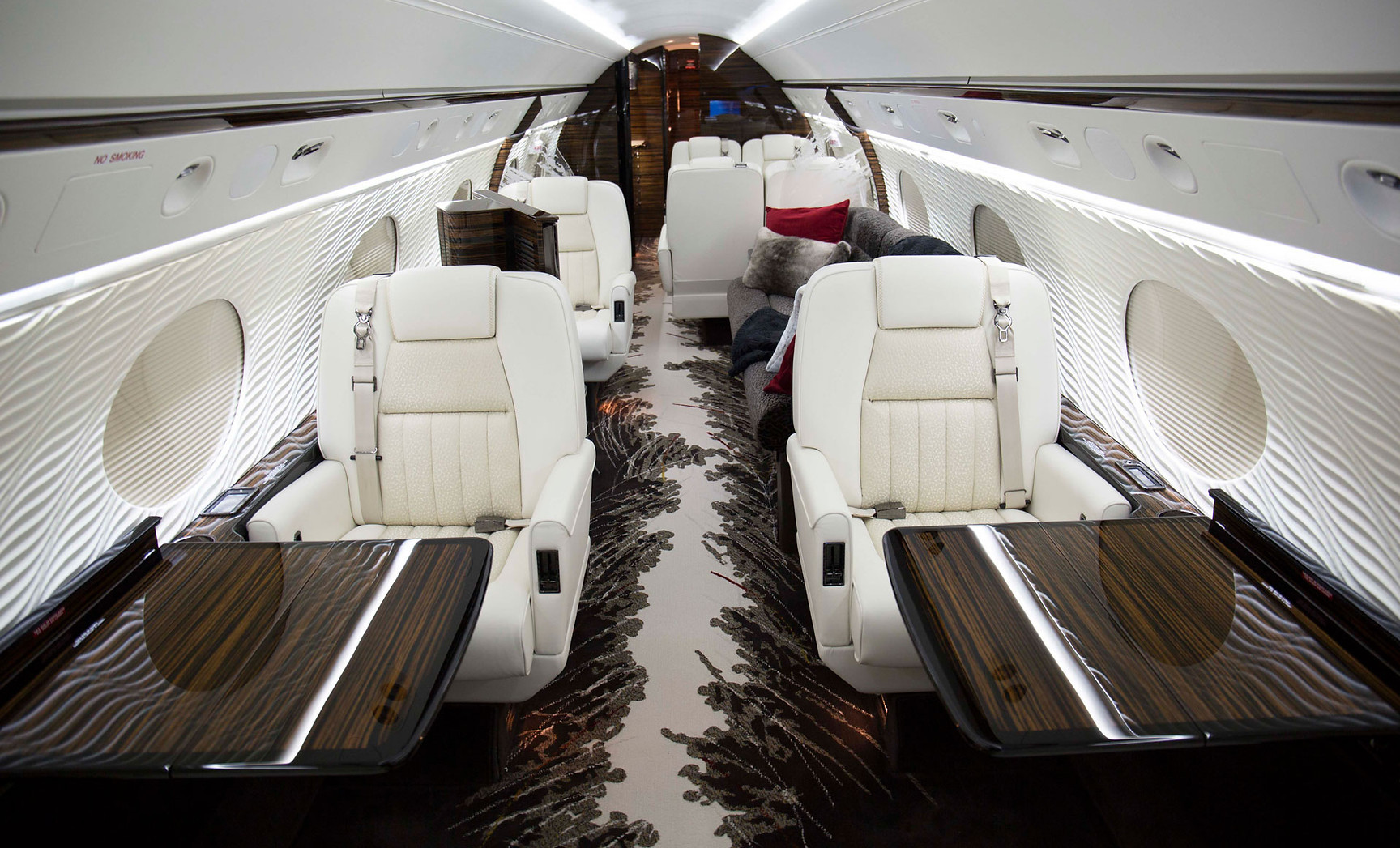
%20copy%202.png)
D E C O R A T I V E S U R F A C E S

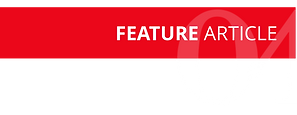%20copy%206.png)
Kalogridis International is a ubiquitous brand in the private aviation space, so I won’t spend time trying to explain who they are and their amazing legacy extending all the way back to the early eighties. But what many might not fully be aware of is their relatively recent spin-off division, Deconel. I was excited to finally get a chance to do this piece because of what Deconel is all about…Custom 3-Dimensional Surfaces. Why is that exciting? Because as a designer myself and as all designers will attest, there are two major components involved in the development of any design.
There is: 1) the Architecture (the physical form) and 2) the Finish Materials. And generally speaking, you tackle the former before moving to the latter. But three-dimensional surfaces are a breed of their own, sort of riding the line in between. That is to say that they could legitimately be thought about as a part of architecture
(hence their 3-d characteristic), as well as finish materials,
because indeed they are that as well.
So in that sense, 3-dimensional surfaces are unique – and virtually anything unique in an interior designer’s arsenal, is of high interest. Another way to think about it is that we have all these elements that have been around since the first interior was ever installed in an aircraft. You’ve got your upholstery leathers and fabrics, you’ve got your carpet, your wood veneers, you plated trims…and so it goes. They’re universal pieces in the jet cabin puzzle and while there are a wide array of color and textural options within each, at the end of the day, they are what they are; some yarn, some cowhide, some wood etc. But 3-d surfaces…well, that’s a whole other animal because as we’ll find out below, they can be wonderful composites of multiple materials melded together creating forms that are anything but flat and anything but boring!
Today I was fortunate to sit down with Deconel’s director, Nichole Kalogridis for a little Q&A session. I love what I learned and for the designers and completion centers reading this, I think you will too.
RR: When was the Deconel division first launched and how did that come about?
​
NK: So, I guess it dates back to when we were doing a lot of airline tapestries for airlines, part of our core offerings – things we can do on our carpet looms. So as an example, we did a lot of things for American and Alaska and those were feature pieces that were used on the bulkheads. But with the flammability requirements, those had to be made out of Nomex yarn instead of wool and around 911 all of the Nomex fibers were getting sent off to the military so we were unable to get that material from DuPont. So my father (George Kalogridis) came up with an idea to replace that material with something that was even more lightweight that and also sound absorbing. And what he found was a different nomex fiber which we had made into fabric – very well suited for our objectives. So we came up with a composite of Nomex fabric and foam for commercial aerospace. So to answer your question, our first Deconel project was in 2006, again with American Airlines doing their bulkheads. And from there, we quickly went more into private aerospace and then maybe six or seven years ago we started coming back into commercial again, this time with carriers like Emirates and Etihad, along with some others. But still doing a lot of private aerospace as well – essentially covering both sectors and not just covering bulkheads but headliners, window panels and dados as well, basically any semi curved or flat surface in the aircraft.
​
RR: As a designer myself, I have long been a fan of three-dimensional wallscapes and surface treatments because highly custom treatments like that offer something fresh – in a way that more traditional materials can’t. Can you tell our readers what goes into the development of these stock designs that I see behind you, and on your website?
NK: Sure. It's really derived from multiple places. Back when we were first starting Deconel, there was a lot of trial and error and so we actually had a few techniques come about from little accidents that would happen and then you know, those little accidents would turn into something really cool so we would then recreate them intentionally. In terms of the designs themselves, I gather a lot of inspiration from my travels – architecture, nature and so forth. Sometimes a customer idea will also spark something and then it's really figuring out of how to make it work and be render well with our materials. Of course, we have to take flammability into consideration so we'll make sure we know what materials are available to use to discover that particular design and then kind of build it up from there, so we've got our standard
procedures and things but depending on the project we'll have to make adjustments or alterations to fit OK yeah understood all right I realize you must display stock designs in order to let your customers understand your capabilities but I also realize that surely many of your designers many of the designers that you work with are seeking something totally custom can you tell us uh what percentage of stock versus custom you have and how the process begins or completely custom design working with a designer well stock to us is really a in stock pattern and capability we don't really stock any goods on the shelf just because there are so many combinations you know just because of the diamond stitch doesn't mean that the fabric and the thread are going to match the customer’s needs.


RR: Actually when I said a ‘stock’ what I meant not like a product but a stock design, something you have created in-house vs. custom. How often do your customers go, hey I really like that. I'll have that versus I want to create something custom?
NK: Oh, I see, so, It really depends. I would say 6-7 years ago 90% of what we did was completely custom either the designer would send us a sketch of photo or a DWG and then you know explain what they wanted it to look like now I would say this year might be 50/50 diamonds are backwards style we do have a couple of our stock designs that are very very popular and it's just about three or four and customers keep reordering those.
RR: I wouldn't have thought it would be that much. Interesting mix.
NK: Yes, and one of those was actually one of those techniques where we were just having a bit of fun and it turned into our best seller.
RR: That's always that's always the way it is isn't it? From the least likely origins. OK so, I can see on your website that all of your treatments meet FAA part 25 burn, or I assume they do, but I'm sure our readers would be interested to know what specific materials you used to produce the surface treatments and perhaps an idea of their installed weight.
NK: Our VVIP Materials pass 14 CFR FAR 25.853(a), Appendix F, Part I (a)(1)(i). Our commercial line of materials passes: 14 CFR Part 25.853 (d), Appendix F, Part IV, Part V. As for weight, our material is very lightweight but to put a finer point on it, most of our installs have a net aero effect – no weight penalty at all.
RR: Can you explain?
NK: Yes, you have to consider that we're not adding anything. In other words, it wouldn't be an additional weight to what you’re already installing in the aircraft anyway because traditionally you're getting a window panel and you're spraying it and then you're adding a foam and then you're spraying it and then you're adding a fabric. We send ours as a complete ready-to-install composite - so you might actually wind up with less weight because we don't use the spray glue adhesive for our composite just because it looks nicer without it. So, often a negative weight yield compared to standardly installed window panels.
Heading 5
RR: I’m sure our readers will be heartened by that. Can you tell us if there are any limitations on the thickness or the depth of a particular design? I'm asking this because I know some designers are seeking a very pronounced 3D effect on bulkheads. Are such exaggerated reliefs within your capabilities? in other words, instead of being maybe 1/4 inch thick, can they be a couple of inches or more?
NK: I would say the thickest we’ve ever done for a window line is half an inch and that was a very 3D design. That thickness of material becomes very difficult to install but it can be done. So, with our particular applications, I don't see a need for anything thicker than that, however we will always take it on if requested. As for minimums, we'll go down to about a 16th of an inch.
RR: Very good, thank you.
NK: Oh, and then answer your earlier question that I avoided unintentionally, related to fabric choices, we actually work with quite a bit so of course your ultra leathers, ultra suedes that sort of thing that's already approved for aircraft. Anything like that is going to go over fine with the rest of the composite. However, we are also able to use some more interesting hospitality materials as well – these added into our aircraft grade foam backings and our FR treatments. Sometimes we don't even have to treat the material but we are able to get our composite to pass with linen - which as you probably know, is kind of marginal. Designers are often afraid of it, so we’ve made some progress there. And then there are also some things like hair-on leather hydes that've been acid washed. Then they have kind of a foil effect, so we really even if a product might be marginal, we'd be happy to test it out with our build up and see if we can get it to pass. We’re not afraid of challenges.

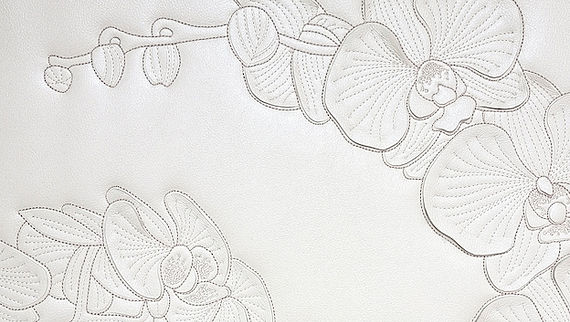
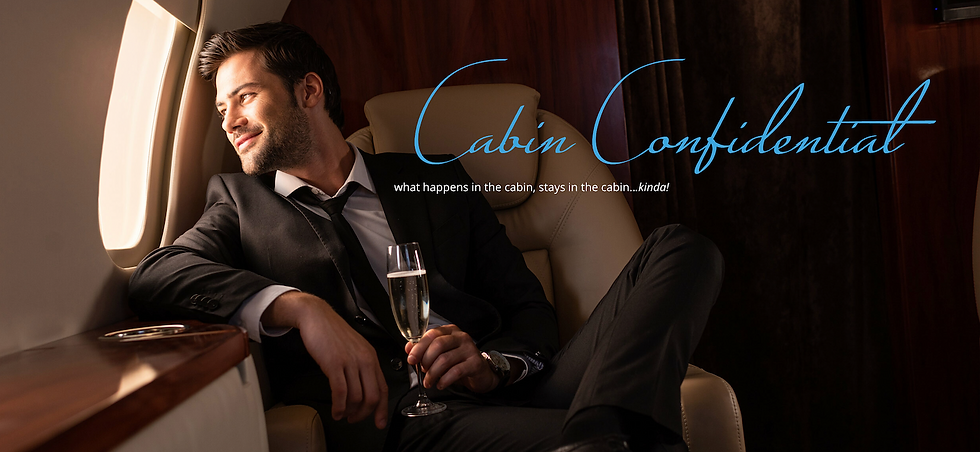
From Cockpit Crew to Cabin Crew. . . the Inside Dope on the Rich & Famous at 51,000 Ft.
Third Grammy Takes a Fall
9:14 am PDT – Van Nuys, CA / Flight Log: June 1st, 2021​
​
Dakota Prescott had just won a third Grammy, was riding the Billboard charts for her fourteenth week straight and for the first time in her career, was no longer awaken by dreams that her car was being repossessed.
In fact, her success seemed so firmly on the rails, she had decided to make good on a promise she’d made seven years earlier. One night following their graduation from NYU, Dakota and her two bestie classmates, Blake and Suzanne, did what they’d done often throughout the prior four years. They all dolled up, grabbed a cab and staked out at The Beauty Bar, an infamous establishment on E. 14th in Grammercy. It had been there since the 90’s and was a compulsory cocktail venue for young women in NYC. It’s mainstay: Super chilled Martinis and fabulous Manicures. But this night in the spring of 2014 was different than the rest. All three were done with school and done with the usual measured sobriety. They had pooled their money, hired a car, and vowed not to leave until they were thrown out.
Somewhere around the third Martini and fully dried nails, Dakota decided she would regale the patrons and her friends with a decidedly up-tempo, jazzed up version of Summertime. There’s no stage in the ‘Beauty’ mind you, but there is a formidable bar on which to stand and by the time she was done, there was another full round of Hendricks Gin martinis standing like soldiers at her feet – on the house! Amid roaring applause and adulation, she promised her two BFFs that, when she won her first Grammy, she was going to treat them all to a decadent, girls only week in Playa del Carmen, Mexico – a favorite spot of the foursome where the tacos were greasy, and nights were breezy.
Seven years later, Dakota was still in shock her career had actually played out as she’d imagined. But her promise had not. She was two Grammys late - and she’d heard about it! Her friends had reluctantly given her a hall-pass for Grammy #1, over her all too tragic LA style breakup with film producer Ryan Meddles. The second had come and gone with no excuse at all and the friendships had grown chilly. But the third she vowed, would not go unfulfilled.
On the advice of her agent, she used one of his contacts at Clay Lacey Aviation in Van Nuys to help her organize a charter aircraft for the total 9-hour return flight to and from Cancun International Aeropuerto. It was going to be a big check, even considering her recent financial successes. But there was egg to clear and she was committed. At the end of the day, she signed on for a 2006 Gulfstream lV – not new by any means, but with a recently retrofitted interior. It had dark carpet, white leather seats and Bubinga wood on the bulkheads. It came with a pilot, a co-pilot, one flight attendant and all the Vueve they could drink.

“And now accepting her third Grammy, please welcome..."

Blake still lived in NY but Suzanne had taken a job just up the coast in Marin three years prior. With the dates all set, Dakota’s manager organized flights and had the pair flown in commercially the day before. They would all meet up the following morning at Van Nuys to join the charter. She’d also decided to round up to a foursome by inviting her younger sister Roselyn, whom they all loved and more importantly, tended to raise the fun meter in any room.
It was a typical LA morning. Weather was clear and 64 degrees. And better yet, the forecast on the Yucatan was 84 degrees sporting a light breeze. It was 8:45 am, when they all four turned up at Clay Lacey. The flight attendant and co-pilot were at the base of the airstair and the APU on the G-lV was fired up with the familiar high-pitched whine. And of course, the wonderful pre-flight aroma of Jet A, present at all busy FBOs.
At 9:14, they were wheels up heading west out over the Pacific coastline, before turning back southeast toward the Yucatan. The flight attendant, Marla, asked if she could start them off with some Mimosas.
Dakota replied, “Perfect, but let’s skip the orange juice.”
They all laughed and snuggled up together at the four-place dining table. The distance from LA to Cancun was 1,841 nautical miles and would route them across the northern Baja peninsula, the Sea of Cortez. Mainland Mexico and the Gulf of Mexico. It was shaping up to be a beautiful flight and the egg was already coming off Dakota’s face with each sip of the bubbly.
At slightly les than an hour into the flight, Ros, Dakota’s younger sister by two years, decided to amp things up a bit. She stood in her chair and using the armrests, crawled out of her seat over Blake, dropping to the floor, a bottle of Vueve in her hand. She stood next to the four-top table and began gyrating to the nineties’ rap song, Hard Knock Life, by Jay-Z. She was gettin’ it done sans any soundtrack, totally a cappella and with the full attention of her audience, who by now were all singing the lyrics at the top of their lungs.
Just as the performance was over, Marla re-entered the cabin from the galley, stopped and planted her fists on her hips, leering at the four.
“The captain has told me to inform you” she announced over a mock PA, “that if you can’t sit down and behave yourselves…he will turn the airplane around!”
They were all surprised for an instant before breaking into laughter.
“Ok, come here Marla, is it?” said Dakota.
Marla nodded.
“So, what’s your jam Marla? I think we need to know your story.”
“So, I’ve never been a flight attendant. I faked my way into this gig so I could go hang out in Mexico with some famous people.”
“Is that right?” said Dakota.
“Yes mam.”
“Ok, so if you’re not a real flight attendant, how did you manage to bullshit your way on here?”
Marla came over and knelt down next to the table. After a quick look over her shoulder, she quietly whispered the words, “I blew the Captain.”
Dakota and her friends erupted in laughter. It didn’t subside for a full minute. Marla looked to be roughly the same age as the rest and she maintained a straight face until the end.
“Ok, Marla, since you ain’t no real flight attendant, I suppose that means you can have a drink with us?”
“Hey, just because I blew the captain, doesn’t mean I don’t have to follow the rules. Sorry ladies, I can’t be drinking any bubbly today I’m afraid. But I can get some music in here and I can bring some crabby snacks and homemades.”
After disappearing back to the galley, Marla bluetoothed her phone to the cabin audio and cued up one of Dakota’s Grammy winning singles, Striaght-up Mama.
As she pulled the curtain and re-emerged, she started the song and pumped up the volume. Dancing her way aft, she made two full turns with a tray of sandwiches above her head in one hand and a fresh bottle of Vueve in the other.
Again, the four broke into laughter and once again they all began to sing at full volume!
But at 1 hour, 21 minutes into the flight, something went horribly wrong. With no warning whatsoever, the plane shot abruptly upward placing more than 2.5 downward G forces on the aircraft and its occupants. Marla and Ros immediately collapsed to the floor. Dakota, Blake and Suzanne were still in their seats but not belted. At that point, it appeared no one was hurt, just shaken up. But before anyone even had a chance to speak, the aircraft again jolted, this time violently dropping, more than a hundred feet – sending Marla and Ros to the ceiling. The other three managed to hang onto the table at least enough to keep from flying out of their chairs.
​


The venerable Boeing 787 Dreamliner will celebrate it's 12th birthday just a few days following this year's NBAA in La Vegas. Since first entering service on October 26th, 2011, Boeing has minted 1,062 copies across three different variants.
But that's not the big story...
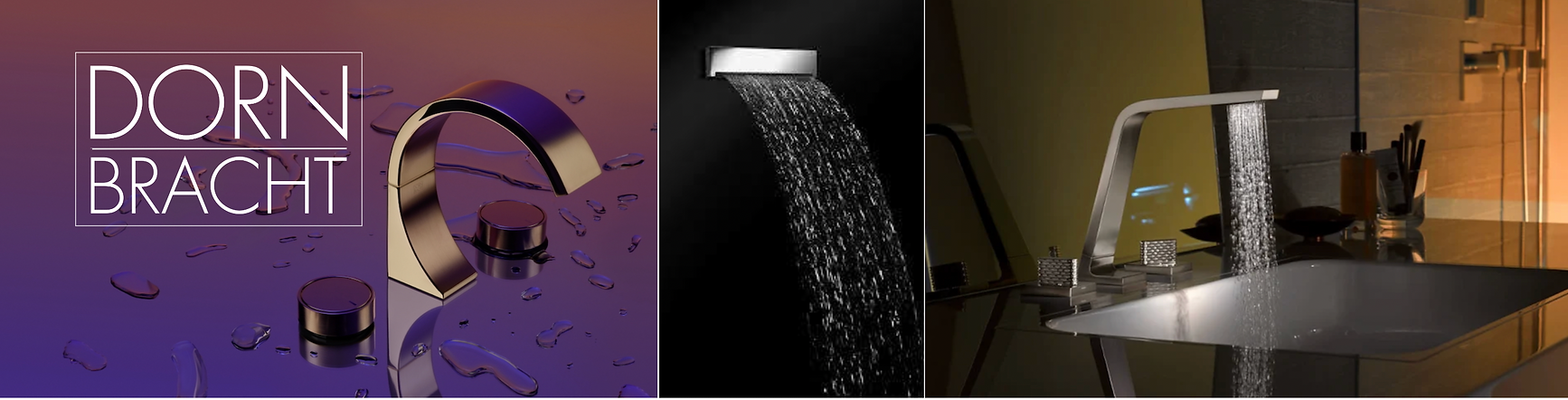

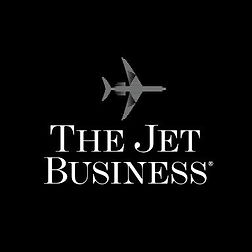
Steve Varsano / CEO
Does your company have something our readers need to know about?


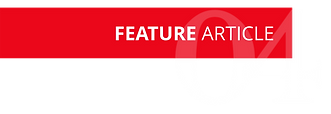%20copy%206.png)

Four Decades of Aviation Artistry
So many tufts...so little time

by Rick Roseman -

Back in 2008, I had a client on a new Gulfstream G-550. From the beginning, the customer had told me they spent much of their time on an island in the Caribbean called Anguilla and that the whole family’s great passion was being by the water. That initial conversation was simply to inform me on how they like to use their aircraft, common routes etc. But the next morning over breakfast at their home in LA and long before ever discussing materials, palette, layout etc., he leaned in with a grin and quietly told me wanted a carpet that mimicked water…WATER.
The next morning as I headed up to Long Beach for our first set of formal meetings with Gulfstream, I called Rich Ruggeri at Scott Group. At the time Rich managed the Dallas showroom and had called on me a couple of times. I had visited their showroom once and remembered being impressed with their product. But even more so with the process he had taken me through in working with designers. I thought to myself, well if these guys are as good as they say they are, let’s see if they’re up to this challenge.

Rich never hesitated. He said, “well it’s not something we’ve done before…but let’s go for it.” We set up a collaboration between myself, my lead designer, Rich and their lead designer in Dallas. I can’t even remember how many meetings we took trying to work out a carpet that truly captured the character and movement of water. We ultimately decided on a 100% silk carpet because as Rich informed, it would come closest to achieving the movement part. “Silk already has a natural undulating quality,” he said, and certainly it does. Silk yarns catch light in a unique way that no other fiber does and of course it has that wonderful shimmer as the pile is caressed or changes direction.
There’s much more to the story but the bottom line is this: In spite of the significant challenges we faced, the project remains one of the most rewarding and fun collaborations I’ve ever head with a supplier. Rich and his team, in close collaboration with their mill in Grand Rapids, must have produced five strike-offs before we hit the right combination of yarn, pattern and palette. But when we finally got there, we all knew – his team and ours – that we had indeed managed to turn loomed silk into an undulating sea!
As is the case with all great jobs, the client never sees what you go through to achieve his or her vision or desires. But as designers, it’s the process itself that is so rewarding and when you realize you’ve chosen the spot-on perfect supplier, it’s that perfect storm that takes you places you didn’t know were possible.
​
My friend Rich Ruggeri has since taken his retirement but the team at Scott Group Studio are still at the very top of their game, with a unique confluence of artistry, know-how and craftsmanship. Today I had the pleasure of sitting down with Alyssa Aguilar, Scott Group’s Marketing & Brand Manager. Below is the result of our informal Q&A.
​
​
JCFM: A design colleague once told me that she regarded carpet as the "foundation" for any successful jet cabin concept. I tend to agree. With that in mind, can you briefly describe our readers what a typical interface is like in working with a designer to find the right carpet design and color palette for a jet project.
AA: We have a team of 9 in house designers and 4 in our Visual Design Department who develop and render the design concepts. We can help provide a starting point or work based off a concept. The starting point may be a physical sample, a pattern selected from our website, or designers may send us their materials to reference for pattern and color. We can start with pom color selection, then develop rendered pattern concepts and from that, produce a sample in the selected color and texture for approval. The process is simple, and our team is very experienced in working with all aircraft platforms and understand their unique specification requirements for design.
JCFM: Your website is full of wonderful designs, but I know that many designers, myself included, often want to create their own custom designs. For VVIP projects, can you tell us generally what percentage of designers opt for "fully custom" vs. "SG Stock Patterns and what advantages might exist for either?
AA: I would say that currently around 10% of designs are brand new fully custom patterns. For an aircraft owner who wants a totally unique design made especially for them, we can work through the new design development process with the designer. We understand that demands on a designer’s time have increased, and we want to help them get to a successful solution. So, we develop new collections with the intent of providing beautiful and relevant designs to serve as a great starting point, where a change of color is all that’s needed, or it may be perfect as shown. Either way, we are well equipped to service a designer’s needs depending on the time they have to work within.

Precision handwork...
...one carpet at a time.
JCFM: I know that most designers are focused on the aesthetic aspects of a custom carpet - but I also know there are many "practical" concerns as well. Can you give us an idea of some of the practical aspects that you often explain to your customers that may govern or affect their design decisions? Can you please explain the difference and what unique effect one might have over the other in terms of look and feel?
AA: Understanding how the aircraft will be used is extremely important to providing the best product solution. If the aircraft has heavy use, we recommend a primarily loop construction in a blend of colors that will hide dirt and soiling. If the aircraft is used less frequently, owned by an individual or family, a designer might want to consider using a combination of softer fibers in cut pile, like silk, or wool cashmere that are plush and soft to walk on. We can also be somewhere in the middle, by using silk or other fibers as accents in the pattern.
JCFM: As far back as I can remember, Scott Group has always seemed to take much of its inspiration from "nature". Is this something that is customer driven or more something born out of your own company culture? Also can you tell us if 'nature' themes are often selected for aviation projects - or does it tend to be more abstract themes?
AA: I believe it’s both. With an increased focus on Sustainability, biomorphic forms in design and architecture are becoming more prevalent. Nature is an amazing place to draw inspiration from for both form and function. We often look to nature, fashion, and interior design for pattern inspiration. Our organic patterns are oftentimes non-repeating and “flow throughout the cabin. The pattern can be designed specific to the aircraft layout and lead the eye throughout the cabin creating a visually interesting and harmonious effect. Organic patterns are also more “forgiving” in the installation process as well.
JCFM: Hand sheared or carved carpets have always held a fascination for me. They are amazingly evocative to the eye and immediately impressive - however it seems to me that in recent years, it is less common. Is this just my own misconception or is there a trend away from such sculptural carpets?
AA: Carved and sculpted carpets are amazing not only in the 3-dimensional effect it creates with the pattern, but also the skill it takes from the craftsperson to execute. We have seen the trend of carving change over the years. In the past carving was used in Traditional patterns to delineate and accentuate pattern elements or to create separation of a border for an aisle. More recently, carving has been to create modern designs where the actual pattern is created by carving the pattern in 3 dimensions. It takes a high level of skill and experience from the craftsperson to execute a carved pattern.
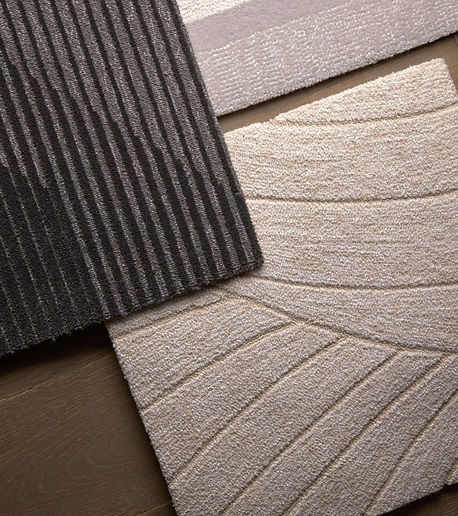

JCFM: I know that one of the most exciting parts of the process for most designers is working with the 'color tufts' to find the perfect palette to match surrounding materials etc. I would assume this is a critical part of the process immediately prior to producing a strike-off. I realize that designers generally know just what they're looking for - but how often do they ask for your help and guidance? That is to say, how often is your vast experience in working with yarns, colors, dyes etc, called upon as you're working with a designer?
AA: We encourage communication between our clients and design team. We find the best results come when we can help guide the yarn color selection process. There are multiple strands of yarn used to create a blend of color. Our team uses their expertise in how color hues and values interact with one another in the construction of a 3-dimensional design. We want to make sure that we are providing the best results and will reach out to the designer if we think we what they are looking for can be better achieved by making slight adjustments to the color. Most designers that we work with are open and appreciative of that level of communication with our SGS Design team. We also understand the importance of color quality and ensuring that the carpet matches the materials and coordinates with the interior.
The US's first Air Force 1 - a Boeing 707 (VC-137B), utilized by Eisenhower, Kennedy, Johnson & Nixon
ORBIT BBJ - delivered fall 2001 / RRAD Design
And low and behold . . . there were plenty of takers!
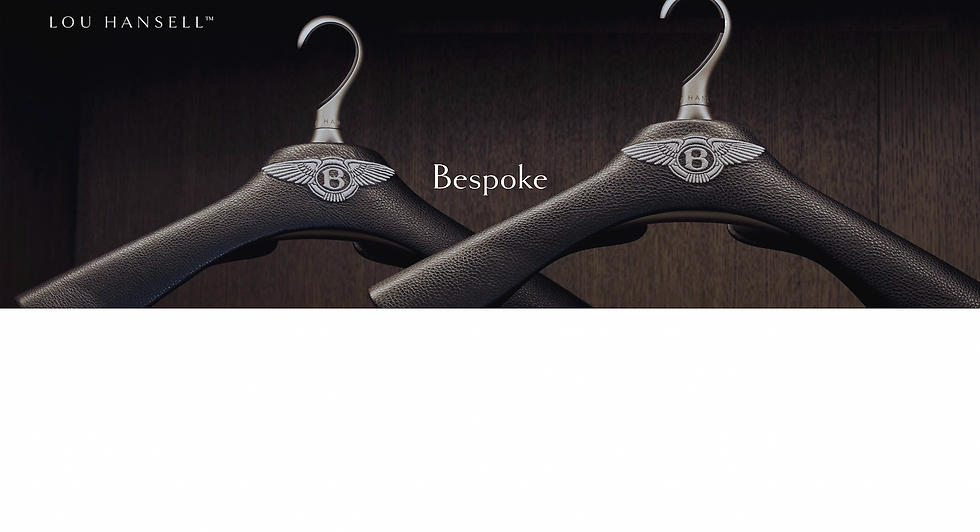
When you open the door to the Lou Hansell Bespoke studio, the possibilities begin. Our artisans and designers have selected a palette of exquisite materials, with 51 shades of ltalian leathers, five metal and inner trim pairings, and personalization options. Driven by their boundless creativity, they combine their talents and craftsmanship to create pieces you’ll cherish forever.
louhansell.com


JCF Magazine celebrates the Global 7000 & 8000 this month, remarkable achievements by any measurement. Watch the video and note that on top of it all, you can breathe easier with Bombardier's PÅ©r Air and its advanced HEPA filter technology, arrive rested and refreshed with the Soleil circadian lighting system, experience the comfort of the industry’s lowest cabin altitude, and enjoy reduced lower back pressure with the Nuage seat and zero-gravity position.
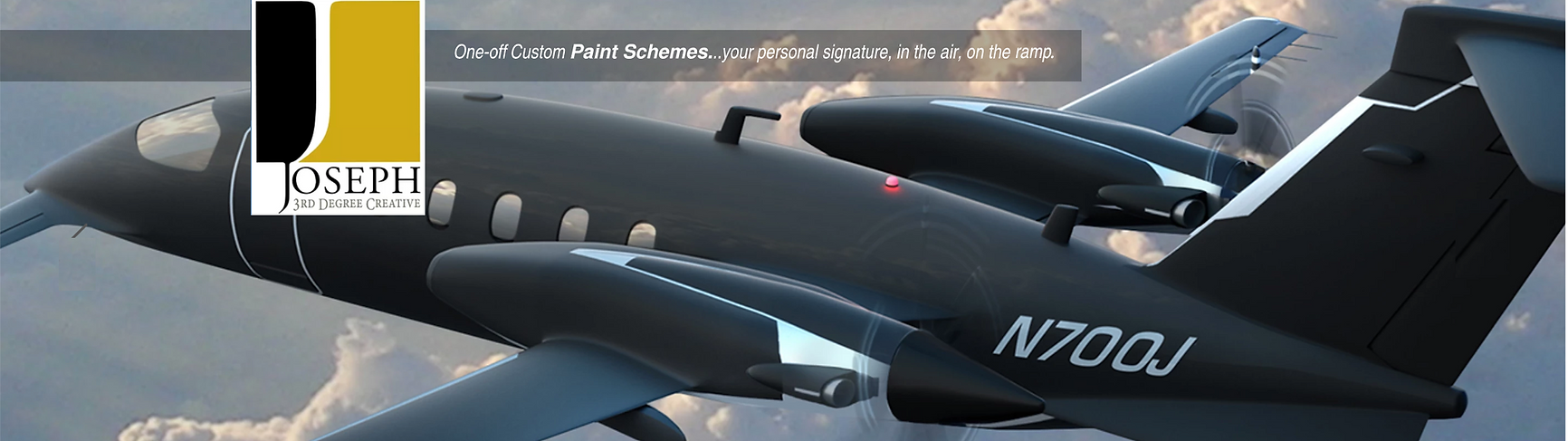
