
A few years ago, I was attending an IDSA (Industrial Design Society of America) conference. In a mixer that followed, I listened to several designers talk about their overall philosophies and approaches to Industrial Design. But one remark stuck with me. A young designer said...
” Brightwork is a required relief between soft goods and other surfaces. The eye wants those embarkations in order to frame and highlight the adjoining materials.”
His term brightwork of course refers to plated metal surfaces and trims. I think it stuck with me because as a designer, I understand and agree completely with his observation. In any interior environment, and especially an aircraft cabin, soft goods and woods generally dominate. Plated metal trims and surfaces that reflect light and therefore capture motion while moving through the cabin, are essential in framing elements and completing the aesthetic. It's a design element that never goes out of style. However they're also highly visible, tactile components that will directly interface with the end user as they travel aboard their aircraft. Each and every component must meet incredibly high-quality standards – holding up to flawless scrutiny. This is where selecting the right resource is so critical, as all platers are not created equally. Tanury Industries is a premier example of such a resource. They are uniquely qualified, possessing multiple certifications in aerospace - and particularly, for components that will reside in the cabin of VVIP and top-tier business Jet interiors.
It was my pleasure to sit down this week with the company’s CEO, Michael Akkaoui and two of its officers, Paula Frias and Martin Buckholtz to learn more about what makes them one of the industry’s premier plating vendors – especially among completion centers and designers. To get there we started with a little background. Tanury Brothers Inc opened its doors in 1946, just at the tail end of WWll. Employing only 12 initially, it was shiny things the brothers knew about, scarcities of the war era. Jewelry, eyewear and freshly minted automobiles would all re-emerge as booming business sectors in post-war America. Beginning with just a handful of clients, Tanury delivered what they needed, when they needed it. And as those businesses grew, so did their own. Like most plating companies of the era, aerospace didn’t come along till much later. But by the time it did,
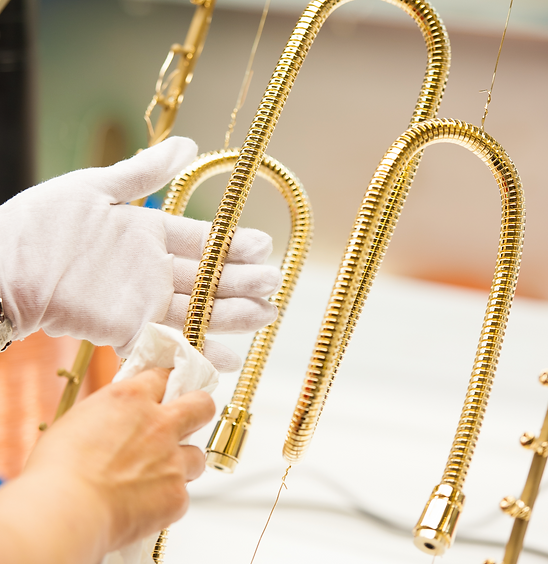
they had become Tanury Industries and had amassed the vast, seasoned experience and technical expertise that would later serve them on entering aerospace. The opportunity finally came about in 2000 when Mr. Buckholtz (a.k.a. Marty), was brought aboard to head the new division – a position he still holds. Needless to say, the division has grown tremendously since that time. Having begun with a single but very large Head of State program, it set the course, and on its heels, several more followed. As we discovered in conversation, Mr. Buckholtz travelled in many of the same circles as myself...many familiar companies and key figures of the day. As we both agreed, there is no better area within aviation to cut your teeth on than VVIP. The level of scrutiny and demand for absolute zero-defect, is unsurpassed in literally any other market – which of course necessarily demands the same of your own internal QC practices and protocols.
In that regard, the company quickly rose to the occasion and currently holds an AS9100-D certification AND its own FAA Repair License (for interior cabin components). In fact, as Mr. Akkaoui described...
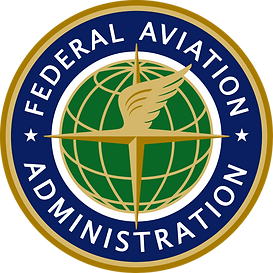.png)
...“We were the first ever plating company to be granted an FAA Repair License and since there was no historical precedence, our own internal process spec was used in drafting the FAA’s governing spec.”
It’s also worth noting that Tanury is NADCAP certified for gold. When it comes to aviation components, Tanury not only has the highest and most complete certifications but provides turnkey parts for its customers – starting with the receiving of raw material, to precision masking, tolerance measuring, plating, clearcoating and check-fit; all so that the completion centers wind up with their returned parts, ready to install parts.
When I asked about anything else that might set them apart from other aerospace platers, Mr. Akkaoui explained they have just now begun offering a brand new, more durable alternative to anodizing, called Cerakote. “We’re the first plating company anywhere to offer this process, and it’s really nice to now roll it out to our customers. Cerakote is a ceramic-polymer technology with sharply enhanced wear resistance – as well as superior corrosion and weather-resistant properties. It’s also a high-temperature product originally developed for automotive applications. According to Mr. Buckholtz, it also does not “fatigue” aluminum alloys as is common with anodizing and is chemical- and solvent-resistant as well. “With over 100 standard color options and custom mixes available, it is a remarkable ‘environmentally friendly’ new product, again raising the bar on what we’re able to provide to our customers,” explains Mr. Akkaoui.
​
In a similar vein, Mr. Akkaoui explained Tanury also offers Physical Vapor Deposition (PVD) coatings. Not familiar with the term, I had to ask. He explained it as a process that applies Titanium Nitrate to electroplated surfaces providing a special hardened surface for high-use areas, such as handrails, seat belts, latches, and thresholds.

In terms of facility, Tanury’s main operations are housed in two buildings, comprising over 100,000 sq. ft. with a current employ roster of 210 team members – and very little turnover. They utilize Business, Quality, and Structural teams forming a contributory employee base.
Mr. Akkaoui further explained their use of bar code tracking throughout every area of their operation and that their QC is very mature, meeting or exceeding all prescribed mandates of their AS9100-D certification. “Additionally”, he added, “We they have heavily invested in technical scanning, at the core of which are electron microscopes used for precision coating analysis – supporting over 100 separate chemistries via Tru-Chem software.”
Adding further to their customer offerings, the company’s FAA Repair certification covers “assembly and disassembly” – yet another important capability, removing what is often an enormous burden to customers, therefore extending their model of true turnkey service.
Mr. Akkaoui concluded our interview by proudly pointing to multiple year double-digit growth for the company – despite COVID related downturns.
​
​
As with most great companies serving our unique industry segment, Tanury's beginnings were humble, but they have achieved steady incremental growth over decades. Tanury Industries is a classic example having spent almost eighty years refining their craft and honing their customer service to meet the rigors of VIP aviation requirements and quality demands. It was Freshbook’s pleasure to get an inside glimpse into this company’s history and its current inviable position in the global landscape of highly specialized providers.
​
“We were the first ever plating company to be granted an FAA Repair License and since there was no historical precedence, our own internal process spec was used in drafting the FAA’s governing spec.”
It’s also worth noting that Tanury is NADCAP certified for gold. When it comes to aviation components, Tanury not only has the highest and most complete certifications but provides turnkey parts for its customers – starting with the receiving of raw material, to precision masking, tolerance measuring, plating, clearcoating and check-fit; all so that the completion centers wind up with their returned parts, ready to install parts.
​
​
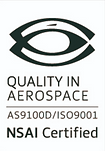

For more info, visit: tanury.com
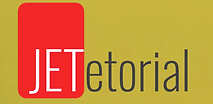
