![Wave Aircraft_1 [high res].jpg](https://static.wixstatic.com/media/38269f_e006b3ba11a645b7967a5a382e970f7c~mv2.jpg/v1/fill/w_980,h_551,al_c,q_85,usm_0.66_1.00_0.01,enc_avif,quality_auto/Wave%20Aircraft_1%20%5Bhigh%20res%5D.jpg)
Siminetti
Specializing in Mother of Pearl

everal years back, I was visiting with a client about their owner’s bathroom in a new Global Express XRS, during the design phase. When we began discussing potential materials for counter surfaces, I could see she wasn’t crazy about any of the samples I had brought along (mostly granites). But a small lightbulb went on and with no sample to support...I blurted the following question.
“Do you by chance like Mother of Pearl?”
She was taking a sip of her tea, but I could see her eyebrows raise. After swallowing, she replied...
“Who doesn’t like Mother of Pearl!?

Needless to say, we wound up cladding every horizontal counter-surface in the bathroom with M.O.P. and she was truly ecstatic when the aircraft delivered! But her reply has resonated with me ever since – because, for the most part, it’s hard to find somebody that doesn’t like pearl. It’s a much less subjective material than marbles, granites, or other stones where the organic pattern options are as endless as a railroad track. They’re entirely subjective. That’s not to say that MOP is right for every space, because it’s not necessarily. But often the playful luminosity and monochromatic qualities of Mother of Pearl are a wonderful, and often overlooked option because they don’t generally compete with other materials in the room. It’s a truly amazing organic material that can lend spectacular results in the hands of a talented designer.
Today I had the pleasure of sitting down with Simon Powell and Lulu Laidlaw-Smith of SIMINETTI, a rather unique company based in Chipping Campden near Stratford upon Avon, (UK) – otherwise known as the former stomping grounds of one William Shakespeare.
​
​​​​​​​​​​​​​Siminetti’s unique focus is on one thing...and one thing only; Mother of Pearl, and to my knowledge, no other company in the world offers more varietals and custom applications. Their client roster reads like the editorial manifest of Architectural Digest or Wallpaper, and their projects range from Superyachts, to high-end Hospitality, to Private Residences...and of course to Private Aircraft.
But this company goes way beyond simply sourcing fine mother or pearl and laying it onto substraights. They have created literally hundreds of unique, proprietary patterns – geometric interlacing designs with varying color hues combined with delicate inlays – each a work of art and each ‘hand-pieced’.
In my conversation with Mr. Powell, (CEO) and Ms. Laidlaw-Smith (Global Business Development Director), I was taken through a unique process that starts with the sourcing of both Freshwater and Saltwater Pearl. The former is sourced from shells that are grown expressly for the natural Freshwater Pearl industry. The shells become a biproduct which Siminetti sources directly from the farms in Asia; the world’s largest producer of Freshwater Pearls, producing some 1,500 metric tons per year. And it’s all fully sustainable. Rather than simply discarding the shells from production after harvesting the pearls themselves, Siminetti sources the shells in conjunction with its partners and are fully utilized to form their shell mosaics and decorative panels. Nothing is ever depleted, and the cycle simply continues without waste or disruption.
![Wave_4 [high res].jpg](https://static.wixstatic.com/media/38269f_3dea9ca0b146420ab0d19278dba92dc6~mv2.jpg/v1/crop/x_3,y_418,w_1064,h_995/fill/w_402,h_376,al_c,q_80,usm_0.66_1.00_0.01,enc_avif,quality_auto/Wave_4%20%5Bhigh%20res%5D.jpg)
Pictured in the Interior image above.
Their Saltwater Pearl is sourced from Pacific communities who depend on sustainable relationships with the ocean lagoons in which they farm pearls or harvest them as a food source. Their suppliers have for generations respected the origin, growth and delicate nature of these shells. Harvesting is done in line with local government fishery laws and a constant communication with their suppliers ensure they are informed and accountable.
But it’s the process and the breadth of flexibility that Siminetti really brings to the table. If you’re a designer considering MOP it’s hard to imagine having a source with more options to support your vision – or that of your customer’s. When asked about former challenges...specs that at the time, were difficult or impossible to achieve, Mr. Powell replied...


When we run into a barrier or impasse...we all sit down and figure a way of solving the issue. There is always a solution, and we enjoy the process of working through challenges.
​​“One such former challenge” he describes “was a problem utilizing large panels of our dry seamed (no grout) mosaics inside shower enclosers. Because our pearl tiles are only 2 mm thick and not otherwise bonded to each other, it allowed moisture to seep behind, which would allow mildew and other issues – meaning it negating our being able fulfill such requirements to those clients. But since that time, we have developed Feature Wall Panels that employ honeycomb sub-straights and water-resistant barriers. We now bond the 2mm mosaic on top, forming the visible surface of a single cohesive buildup, ready to install. It’s proven an excellent solution.”
Ms. Laidlaw-Smith explained they can also apply their mosaics and Feature Wall Panels to ‘curved’ surfaces as well, both outward and inverted, within reasonable radius limitations, affording a wide array of design possibilities and substraight applications.

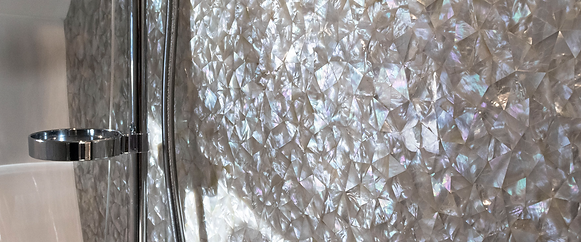
Siminetti offers two basic types of edge joining with their Feature Wall Panels. The first is with metallic edging trims and produces a uniform look between each surface panel. The other, called Alignment is a smooth butt joint with no bonding and with each panel pattern matched to ensure continuity. Each achieves a different look of course; the edging trims rendering a more traditional look and the Alignment offering a cleaner, modern appearance. Beyond that, the options are almost endless with literally dozens of styles and patterns to choose – not to mention custom requirements, which the company welcomes.
Siminetti is an SBID 2021 Design Award recipient.
For more info, vist: siminetti.com



F-List
Specializing in Organic Stone Veneers
By : Michael Olengard

/ LIST is known the world over when it comes to aerospace interiors, and in particular, VVIP and top-tier business jets. But because they have such a large and diversified footprint, it’s sometimes hard to keep up with all they do. Stone veneers is a good example. I don’t think it’s widely recognized, especially in the US, that F/LIST has a very robust stone veneer offering across multiple applications.
I had a chance to visit with Dieter Franz, Head of Sales & Customer Relations, Business Unit Air New Market, for a little Q&A.
FB: I started by asking him to take me through their production process from the time the raw material arrives to them. He responded with a very the precise chronology of events below.
“Our stone veneer begins its journey in a very similar way to any stone surface you may see in a residence, yacht, or hotel room for example. The stones originate in a quarry and arrive to us in a slab format.”
“Imagine a one-inch granite slab, it is sawn on the horizontal axis into two pieces and then a backing is applied. These slabs always measure 4 x 8 feet (122 x 244cm) and those are the dimensions we work from generally. For each aircraft project we anticipate needing two or three of the standard slabs. The biggest drivers of selection are linked to the characteristic of the slab e.g., the veins, colors, shading, all contribute to the decision-making process.”
“Once the stone is selected for a project, we begin preparing the stone for the customer.The stone veneers are thinly milled stone that is fixed to a special backing which is then attached to a substrate that ensures it remains solid and prevents crack. The thinnest stone veneer is 0.8mm, any thinner than this and the stone veneer is not strong enough to absorb impact.”
“The optimal depth of the stone veneer countertop is 3mm, and 95% of our projects consist of this. At this depth it is possible to walk on it, place a coffee cup on it, work on it, it is a practical and durable depth. The thickness of the veneer will also depend on the stone and the application. For example, granite is strong so can be milled more thinly than marble which is very soft. It may be that a customer would opt for a granite galley countertop with drip-grooves milled in and will choose a marble accent in a door trim.If the stone is destined to be used for an inlay, a decorative purpose on a table, or bulkhead for example then it is possible to use stone milled to 2mm.”
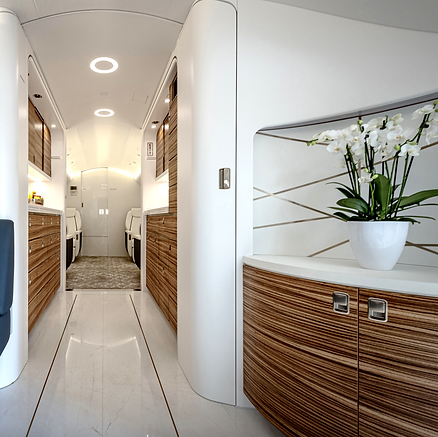
“Depending on the complexity of the project this will take between 3-4 weeks of engineering to prepare the stone for the design. This is followed by production which ensures the veneers are fixed to the substrate, before leaving for the customer. Each ship set is accompanied by data that we have prepared so the completion center or OEM can proceed with any necessary Supplemental Type Certificate work.”
“We hold a standard collection of stone veneers which are refreshed at least every two years to ensure they meet with trending designs. In addition, there are one-off projects where a client will require a very specific color, pattern, or texture and invariably we will visit our contacts – often in Italy – to select the perfect stone. Our aim is always to make the stone veneer strong enough to fulfill its purpose, but light enough to reduce aircraft weight.”
FB: In your opinion, what the potential advantages of stone veneers are, when compared with traditional materials?
“Our stone veneers deliver significant weight savings for customers which is why the owners/completion centers recommend using them. For example, on a large cabin aircraft the stone veneers can help make savings of up to 20 lbs (9 kg) when compared with traditional counter tops. This contributes to reduced operating costs while retaining elegance in the cabin area.”
“The stone veneers are strong, durable and relatively easy to maintain. We have developed a system that looks very similar to the stone countertop you may see in a residence, but in reality, it is a very thin veneer on a lightweight, but strong, substrate so enables multiple design options.”


With our Illuminated Surface System, we have taken the stone veneers and added the dimension of light.
“With our Illuminated Surface System, we have taken the stone veneers and added the dimension of light. This enables light accents around the cabin interior. Behind the galley surfaces, around bulkheads, at foot level in bathrooms amongst others. We’ve also developed a technique where we integrate a heating system beneath the floor and this is very popular with our stone floor customers.”
“There is always movement in the fuselage so we have designed and built-in a foam edging that absorbs some of the flex. Our research and development team devoted time to ensuring that the construction of the stone substrate can flex with the aircraft movement.”
FB: How are your stone veneers installed and fixed?
“The overall composition of the stone veneers has been developed to enable the handling required to fit them into the designated areas of the aircraft. F/LIST prepares the cuts, so all the installers have to do is follow the instructions we provide and fix them into place.

The ease of installation depends on each individual customer and project, but most of the product is in plug and play form. If the stone is destined for an OEM then we will invariably provide specific instructions and where needed will ensure to have teams close by that support the installation if required. This tends to be the norm for the more regular stone veneer projects. Stone veneer countertops are relatively straightforward to fix and use familiar screw fixings that are applied from beneath the holding cabinet into the countertop, so they remain hidden.
One-off projects will be supported by an onsite team to support any complexity of installation. For example, the fitting of a stone countertop and the installation of a shower unit. The veneer is normally kept safe by a protective film, but should a scratch occur – it happens mainly in handling - we can normally fix it onsite. We also help the completion centers, OEMs, and final customers to maintain the stone veneer by providing a dedicated maintenance and cleaning set.
The stone floor is easy to install and remove through a simple click and place type function. This simplicity contributes to lowered completion budgets, and also makes it easy to remove to restore the surface following wear and tear. The solution is popular as it is durable, stain resistant, and hard wearing.
How do designers and completion centers specify and utilize your veneers?
“Our color ranges are numerous which provides the designers and completion centers with a multitude of options for creating unique and personalized designs in the aircraft. In addition, for the more familiar placement on countertops, flooring, and bathrooms the stone veneers are strong enough to be cut into specific shapes to fit into accents and trims on tabletops, bulkheads, or doorway trims for example. This flexibility brings new decorative options to the aircraft for both the designer and the completion centers.”
​
​
Visit F-List at: https://f-list.at/en/
​
​
E-mail: Dieter Franz d.franz@f-list.at

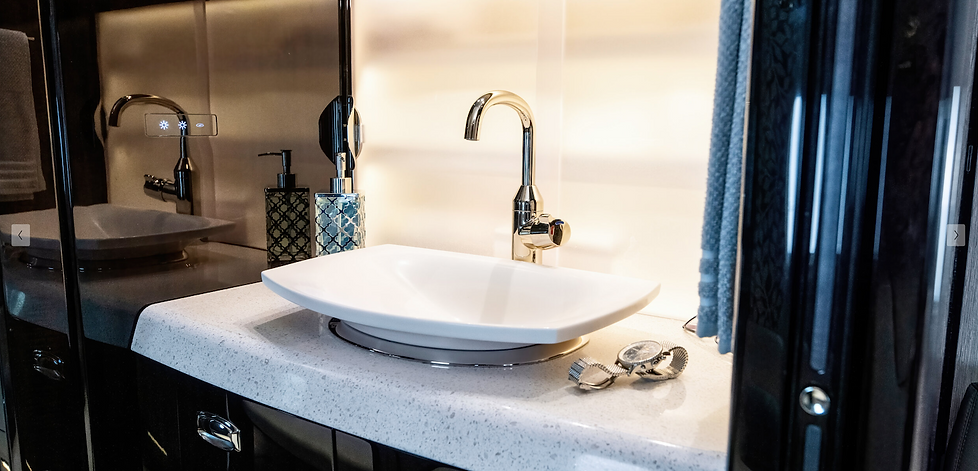
LIPKINS
Specializing in Organic Stone Surfaces
by: Leslie Anne Fuquay
If you’re an aviation designer or completion center in the US, you are likely well familiar with the name LIPKINS, more formally known as SJ Lipkins & Company, in Farmingdale, NY. Since 1971, LIPKINS has been the global leader in lightweight stone surface technology for business aircraft interiors.
The company was originally founded by Stephen Lipkins in 1971 and was eventually handed down to his son Jonathan Lipkins in the late eighties. Until recently Jonathan was the face of the company. His soft-spoken voice was familiar to many of us, as he directly worked with clients on virtually all projects, myself among them. Jonathan never shied away from a custom requirement and we threw more than a few challenging ones in his direction. The end result was always spectacular and the quality always flawless.
Recently Jonathan opted to slip into a well-earned retirement. He ultimately chose to sell the company, which of course keeps the great name and resource around for all of us. Mr. Seth Newman is the company’s new owner and CEO.
LIPKINS has produced over 2,000 countertops for leading aircraft manufacturers and completion centers since its founding. Their precision ‘tiled’ stone veneer is now known as Cloudstone, weighing only one pound per square foot, yet looks, feels and sounds like solid stone.
The secret of the weight savings and flexibility of Cloudstone lies in the unique process LIPKIN’s employs. Their surfaces are comprised of separate precision fit stone tiles bonded to a substrate and then finished as one uniform surface. Lipkin’s artisans carefully create a completely natural appearing design pattern by utilizing the available color and grain in the stone itself. Upon completion, the seams are virtually invisible, and the surface is as smooth as the original slab. The unique process allows them to make the stone extremely thin, yet durable. The technique enables the entire counter top to flex along the
seam lines without cracking.
This unique proprietary process enables LIPKINS to “wrap” stone around a radius profile substrate to follow both simple or compound radii. Popular uses for the process include bullnose moldings, backsplashes, and circular or oval sink cutouts. You can now have the look of thick natural stone at a fraction of the weight with LIPKINS Cloudstone.
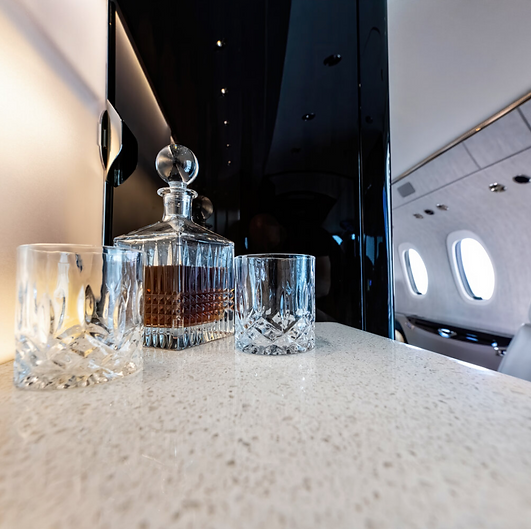
Lipkin’s fabricates their stone surfaces directly onto the substrates supplied by the completion center cabinet shop. This way, the substrate can be check fit prior to stone lamination thus ensuring a correct fit during final assembly. In addition, it eliminates the need for a secondary substrate which would add unnecessary weight.
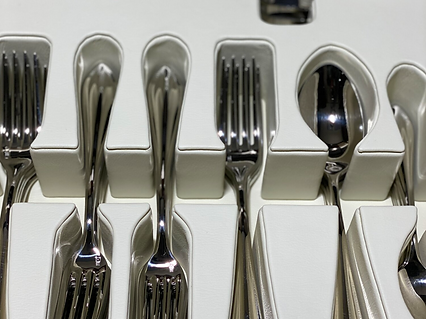
There is zero limitation in your choice of stone. Lipkins always maintains a large inventory of marble, granite and quartz. If additional materials are requested, their relationships with the world’s leading stone importers and distributors ensures that virtually any requirement can be met. Alternatively, the designer or customer can select a material from their own source if desired. LIPKINS will then purchase the slab and have it shipped to their facility for fabrication.
LIPKINS Cloudstone combines the finest craftsmanship with cutting edge weight reduction technology for a beautiful, long lasting, durable surface.
In addition to stone veneered surfaces, Lipkins now offers Flightique, a uniquely compatible product to support the further outfitting of galleys – Galley Organization. LIPKINS will custom design a storage solution to the particular aircraft drawer configuration and fabricate leather or ultra-leather wrapped hard foam organizers to fit your customer’s collection of china, crystal, flatware and serving dishes.
Lipkins can also accomplish stone veneered flooring and other interior accents.
​
​
Visit LIPKINS at: lipkins.com
